Table of Contents
What does the term ” serviceability ” mean in the context of a gas installation? What are the relevant technical principles and regulations? When must a serviceability test be carried out and who carries out this test in the first place? In the following, we would like to clarify these questions and go into important aspects of the serviceability test.
Gas installation and TRGI
First we have to define what is meant by gas installation. The central regulation and a very good reference work for this is the worksheet DVGW G 600 “Technical Rules for Gas Installation” – TRGI for short. This describes that the gas installation includes all components from the main shut-off device (HAE – from German Hauptabsperreinrichtung to the discharge of combustion products into the open air. It thus consists of piping systems, combustion air supply, gas appliances and, if applicable, exhaust systems. For the purposes of this article, we will only consider the pipeline system. It consists of pipelines, i.e. pipes and their connections and the necessary components, e.g. fastenings for the pipes.
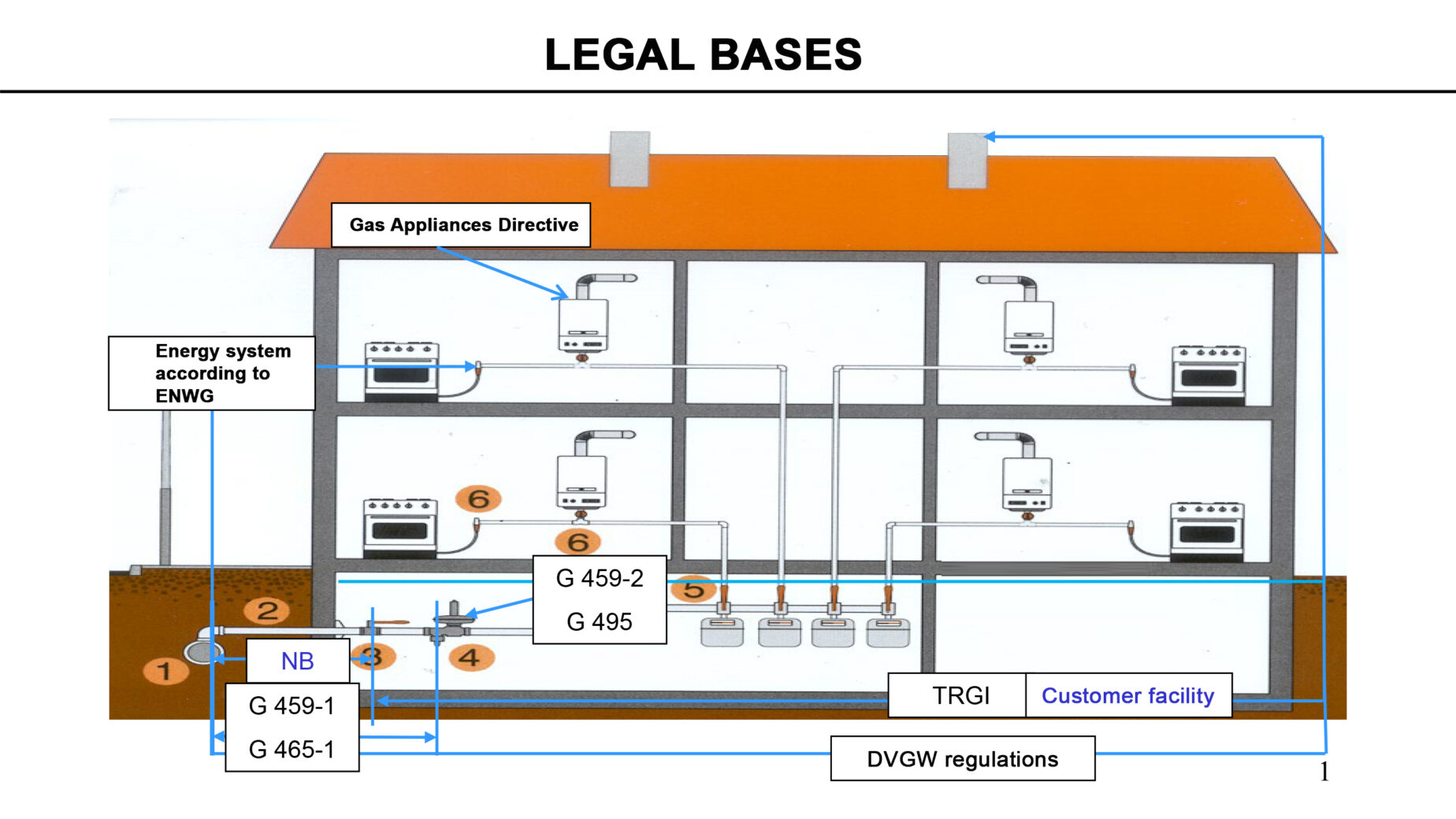
Source: Holger Schröder, Netze Duisburg GmbH
Serviceability and leakage measurement
Testing a pipeline system for serviceability is sometimes reduced to measuring the leakage quantity, which in practice is often referred to as ” calibration “. The gas leakage quantity of the pipeline system is usually determined in litres per hour with the help of a leakage measuring device. In addition to the measurement of the leakage quantity, however, the assessment of the externally visible condition and the functionality of the components are part of a complete inspection for serviceability.
It should be noted that the concept of serviceability and the associated criteria may only be used as an independent test criterion for in-service inspections for systems with operating pressures of up to 100 hPa! Pipeline systems in operation with operating pressures of more than 100 hPa up to 0.1 MPa are tested for leaks with the help of gas detectors or foaming agents.
Furthermore, we have to distinguish between pipeline systems in operation up to 100 hPa and newly laid and repaired systems. The leak test criterion also applies to both. However, depending on the type and scope of the repair, a leakage measurement can round off the result of the work in the case of repaired systems. The serviceability criteria are listed and clarified in the following.
- Unrestricted serviceability exists if the gas leakage quantity at operating pressure is less than 1.0 litre per hour and there is no additional defect.
- Reduced serviceability is defined as a pipeline system whose gas leakage rate at operating pressure is equal to or higher than 1.0 litre per hour and lower than 5.0 litres per hour.
- No serviceability exists if the gas leakage quantity at operating pressure is equal to or higher than 5.0 litres per hour.
An example to illustrate the statement “no additional defect”: If the system to be tested is heavily affected by corrosion or the gas meter shut-off device is defective although the determined gas leakage quantity is less than 1.0 litre per hour, it may be that an unlimited serviceability is not given. It is the task of the specialist on site to assess this.
An exception to the serviceability test is a perceived smell of gas. If this is detected, the cause of the gas odour must be determined and eliminated immediately. In this case, the criteria described should not be applied.
Device types and classes according to DVGW G 5952
As already mentioned, the gas leakage quantity is usually determined with a leakage quantity measuring device. Various types of devices are available on the market, which are divided into four classes in the DVGW Technical Test Specification G 5952.
- Class D: Pressure drop measuring devices for determining the gas leakage quantity based on the measured pressure drop
- Class L: Leakage measuring devices for direct measurement of the gas leakage quantity
- Class V: Volume measuring devices for determining the gas leakage volume on the basis of the measured pressure difference with simultaneous supply of a defined volume to keep the pressure constant.
- Class S: other measuring devices which do not fall under the aforementioned classes.
In practice, a class L measuring device provides the most precise and often also the fastest results due to the direct measurement of the gas leakage quantity via a volume flow or mass flow sensor (as opposed to calculation via e.g. pressure drop).
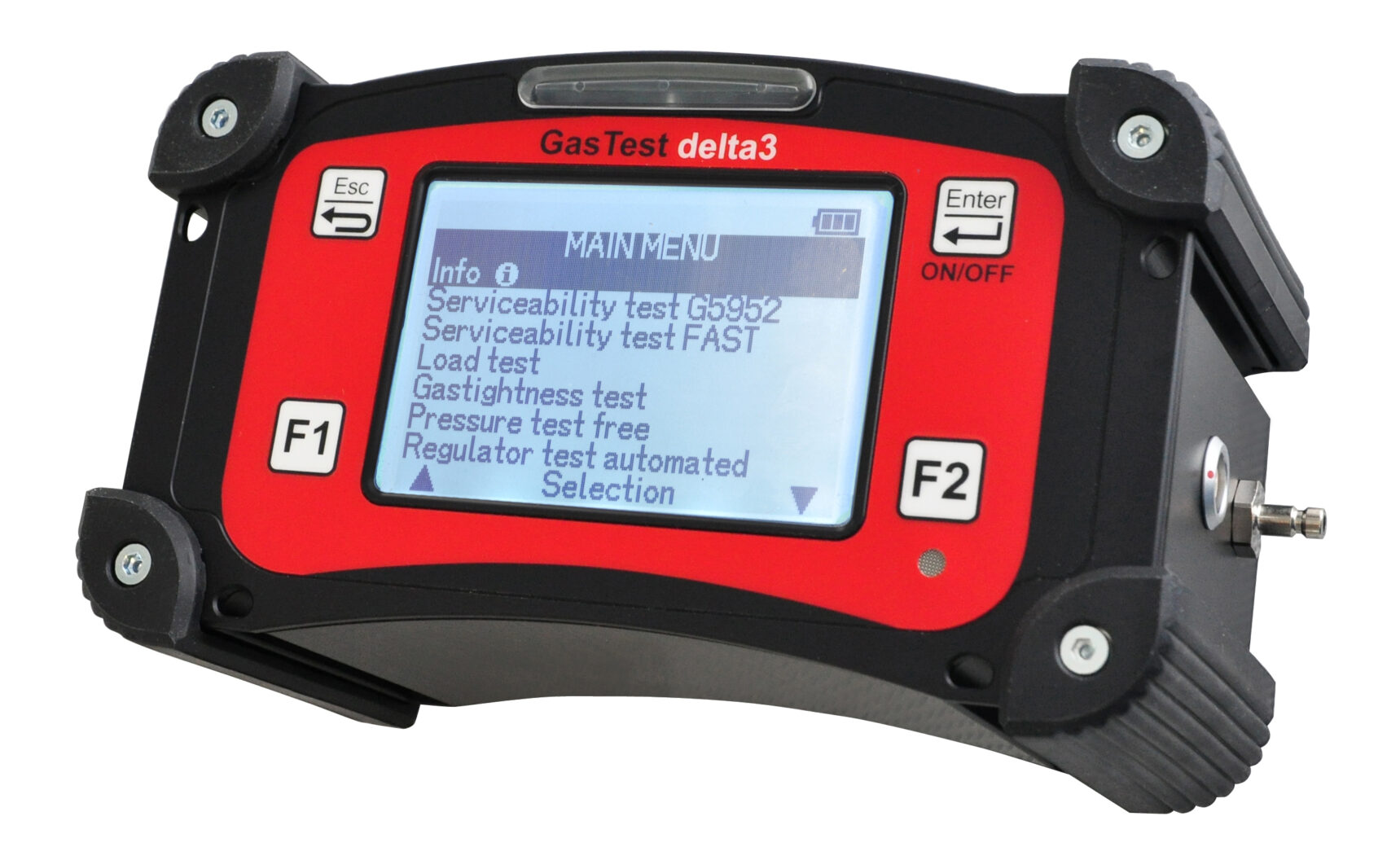
When should a serviceability test be carried out and what measures, if any, should be taken?
The responsibility for commissioning the inspection lies with the operator of the installation, which is usually the house owner. As part of his duty to ensure safety, he must ensure that he or an authorised person carries out a visual inspection of his gas installation at least once a year and has the pipeline system checked for serviceability every 12 years. The latter is occasionally also carried out by the network operator on behalf of the operator of the installation. In contrast, the contract installation company (VIU – from German Vertragsinstallationsunternehmen) or specialised service companies, which must also have a VIU registration, are predestined for this work.
In practice, it also happens that a serviceability test is additionally carried out within the recommended 12 years, e.g. as part of a scheduled meter or regulator replacement by the network operator. The aim of this is to ensure, after completion of the planned measures, that no unintentional leaks have occurred in the pipeline system during the work that would conflict with the required operational safety of the gas installation. The inspection for serviceability is thus also a safeguard for the executing company towards the client or operator of the gas installation. Therefore, the term serviceability is a binding standard for work to be carried out on the gas installation.
History TRGI
The term was introduced for the first time in TRGI 86/96 and with the publication of TRGI 2008 it was raised to the status of an official independent test criterion for recurring tests on systems in operation. However, the term already originated in the course of the conversion from city gas to natural gas at the beginning of the 1970s. At that time, however, it was still in DVGW Code of Practice G 624 “Subsequent sealing of gas pipelines”.
If, after the inspection, the system is found to be serviceable without restrictions, no further measures are required and it can continue to be operated. If the serviceability has been reduced, the system must be repaired within four weeks of the determination. All serviceability tests must be documented in a test report. This documentation must be handed over to the operator. The operator is also responsible for any necessary repairs within four weeks. If the system is no longer serviceable, it must be taken out of service immediately. Under certain circumstances, this can lead to annoyance and incomprehension on the part of the operator, especially in winter, when the heating system cannot be operated any longer as a result. However, there is no alternative to this measure with regard to operational safety.
Serviceability test protocol
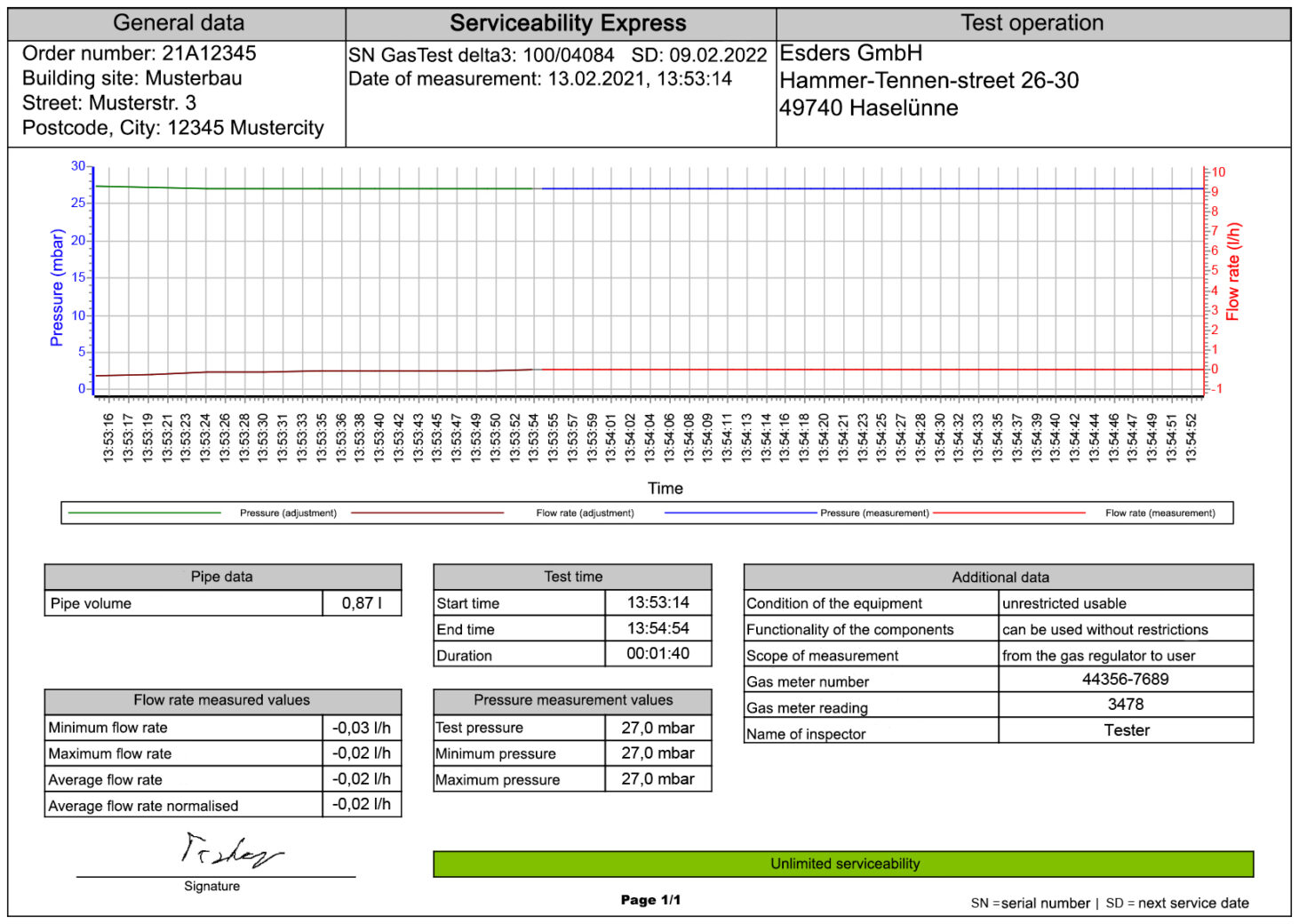
Finally, an interesting piece of information:
An expert report commissioned by the DVGW from the Gas Heating Institute (GWI – from German Gas-Wärme-Institut ) in Essen has confirmed that the majority of pipeline systems in Germany are in a safe operating condition. We would like to back up this statement with a non-representative evaluation of the leakage volume measurements carried out with our measuring devices. This result is not least due to the regular inspections and the underlying regulations and should be consistently continued in the future.
Evaluation of leakage measurements between 2017 and 2020
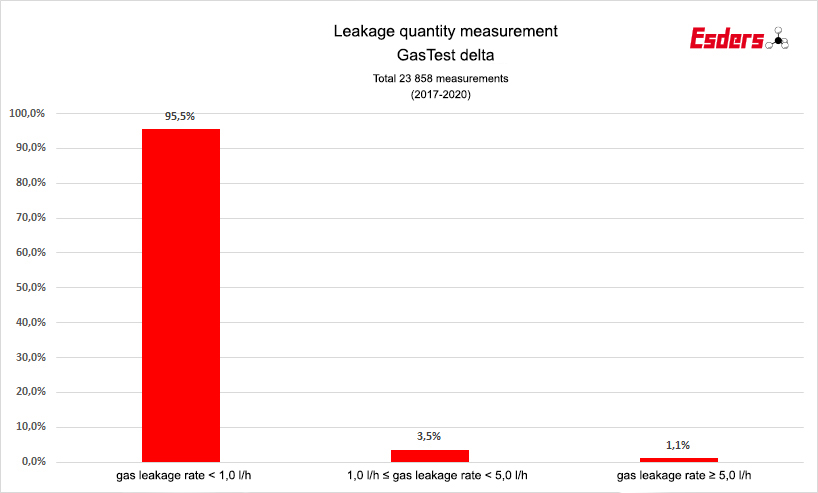
In the next blog post, we discuss how the serviceability test, in particular the leakage measurement, is carried out in practice and what needs to be taken into account.
This blog post was written in close cooperation with Mr Holger Schröder, Netze Duisburg GmbH. We would like to express our sincere thanks for the support.