Table of Contents
In our article of 09 June 2020 on the use of existing measurement technology in gas networks with hydrogen components, we dealt with the properties of hydrogen, the suitability of different sensor technology and the explosion protection of the devices when used in natural gas-hydrogen mixtures. In this article, we want to tie in with the explosion protection of the devices and deepen this topic due to its actuality.
Every gas measuring or gas warning device that is intended for use in potentially explosive atmospheres in accordance with the ATEX directive and is certified accordingly has its own marking that is visible on the device. It contains various information relevant to explosion protection. Using the marking of our gas measuring & gas warning device OLLI as an example, we would like to clarify what is behind it.
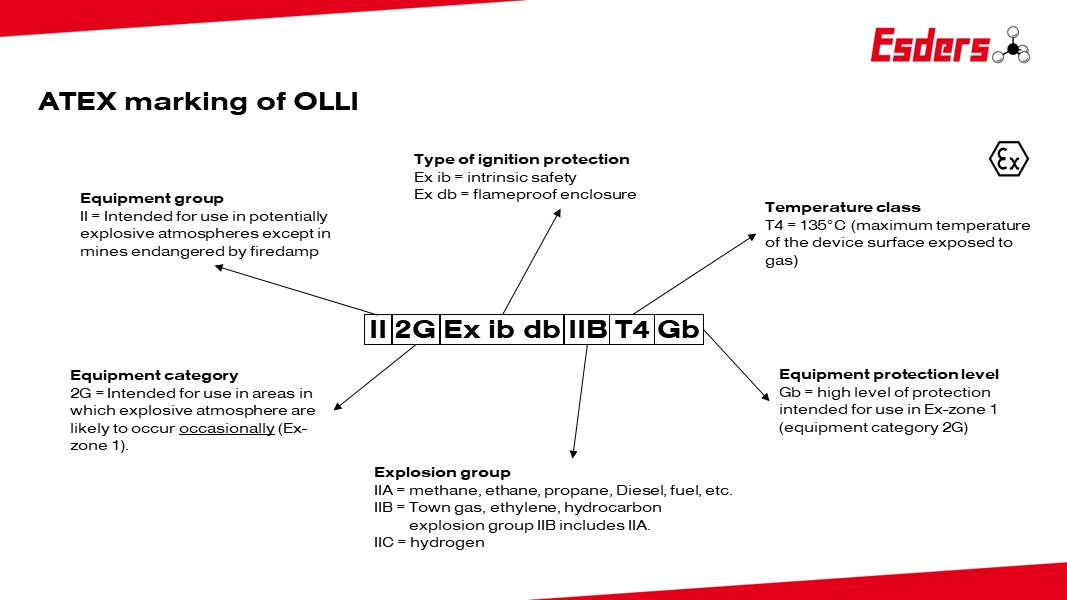
Explosion group
One component of the marking is the explosion group. Gases and gas mixtures are divided into three groups for practical explosion protection.
- IIA: This typically includes gases such as methane, ethane, propane, etc.
- IIB: This includes ethylene, hydrocarbon and gas mixtures such as town gas, which could contain up to 60% hydrogen by volume.
- IIC: This includes e.g. pure hydrogen.
The higher explosion group includes the lower explosion group, i.e. IIB includes IIA.
Maximum safe gap and minimum ignition energy
In view of the agreed climate protection targets, hydrogen is being added to more and more natural gas networks in Germany. In the beginning it was < 10% admixture, with the current version of the DVGW worksheet G 260 (gas properties) up to 20% are possible after individual case assessment and in the meantime, there are already first (test) networks or research projects with 30% admixture. The question therefore arises into which explosion group these natural gas/hydrogen mixtures must be classified and which criteria are used for this.
In the field of electrical explosion protection (one can also speak of ignition protection), the determination is made via the so-called standard gap width and minimum ignition energy.
- The maximum experimental safe gap (MESG) is used to determine the ignition capability of a gas mixture that escapes through a fixed gap. The MESG is the gap width at which ignition of the mixture is no longer possible after it has left the gap. It is determined in a standardised procedure for different gas mixtures.
- The minimum ignition energy is the minimum value of electrical energy that just ignites a gas mixture in the most ignitable composition. For this purpose, the ignition capability of gases is determined in a standardised procedure with a standard current circuit. The determined minimum ignition current in relation to the minimum ignition current of methane results in the minimum ignition current ratio (MIC – Minimum Ignition Current).
Maximum safe gap and minimum ignition current
When classifying gas mixtures into the explosion groups mentioned above, the maximum safe gap and the minimum ignition current can be regarded as equivalent. There is a functional relationship between the two quantities so that they can be converted into each other. For this purpose, the Physikalisch-Technische Bundesanstalt (PTB) has published a report in which the following graph was presented.
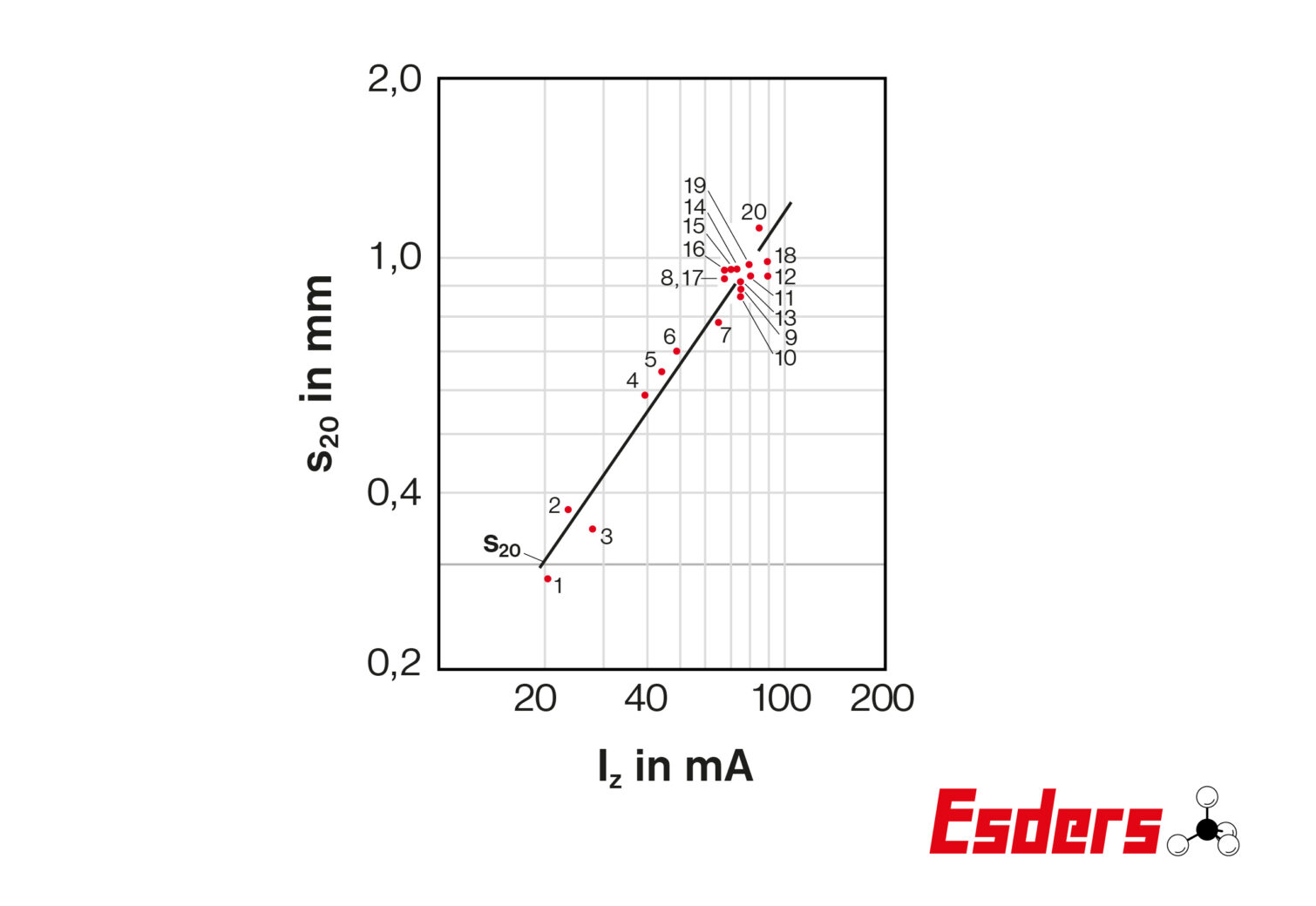
This means that both the maximum safe gap and the minimum ignition energy or minimum ignition current can be used to classify gas mixtures into explosion groups.
For the sake of completeness, we will also show the relationship between the three quantities.
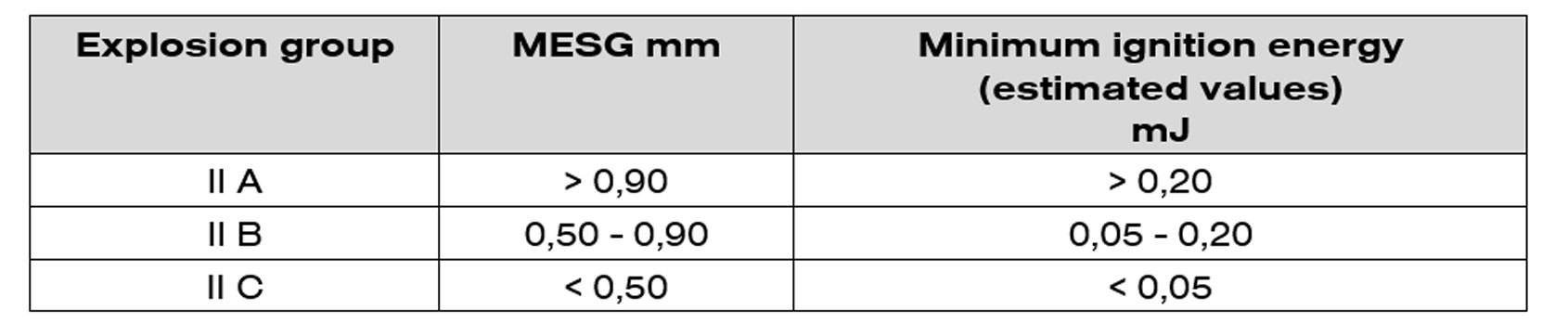
Research project on hydrogen in the existing natural gas grid from 2015
Let us return to the increasing proportion of hydrogen in the existing natural gas network. In 2015, the Federal Institute for Materials Research (Bundesanstalt für Materialforschung – BAM) carried out a research project on this topic in cooperation with DBI Gas- und Umwelttechnik GmbH and with financial support from BG ETEM, and published a final report on it in 2016. The report Sicherheitstechnische Eigenschaften von Erdgas-Wasserstoff-Gemischen (Safety properties of natural gas-hydrogen mixtures) is available for download on the BG ETEM homepage.
One of the questions investigated in this project was the extent to which the addition of 10 vol.-% hydrogen to the natural gas already affects the MESG and thus the explosion group of the natural gas-hydrogen mixture. No significant differences were found, so that the classification in the lowest explosion group IIA is still valid. In the PTB, the MESG of hydrogen-methane mixtures was investigated with an identical apparatus and made available to BAM for the research project. In both cases (natural gas & methane), explosion group IIB was only reached from an addition of about 30% hydrogen. The tests were carried out with different proportions of hydrogen up to 100% with both natural gas and methane. The results can be obtained from the two graphs.
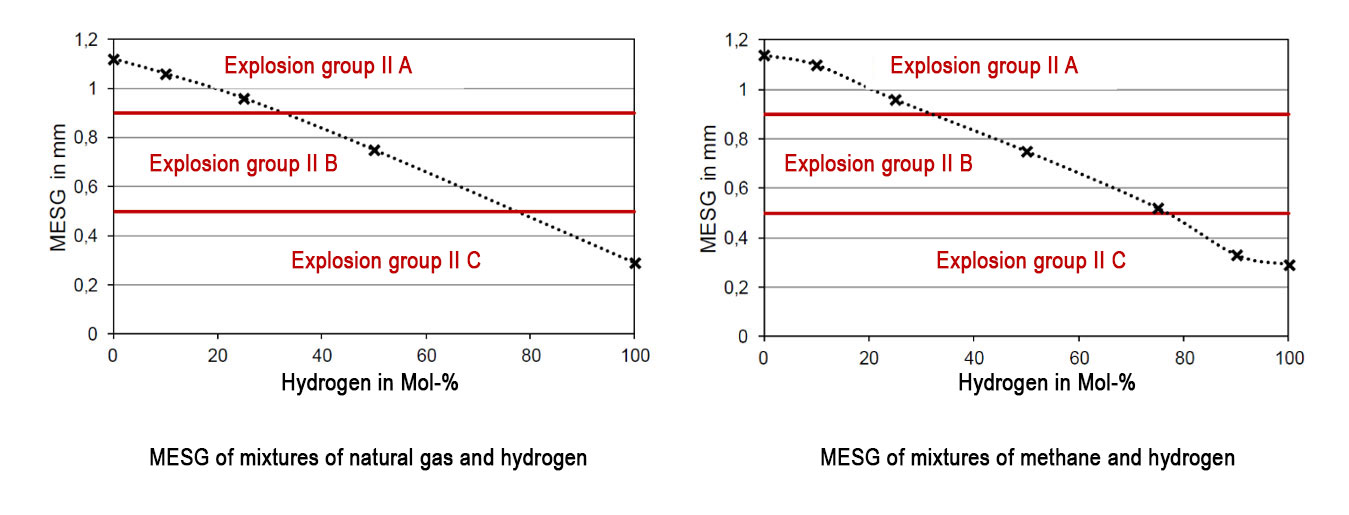
On the basis of these results, it can be stated that explosion group IIC is reached only when about twice the amount of hydrogen is added to the natural gas than planned with 30% addition (i.e. from about 60% by volume).
Type of Ignition protection
In addition to the explosion group, the type of ignition protection is another component of the marking of gas measuring and gas warning devices. There are different types of ignition protection, such as e.g.
- Device protection through flameproof enclosure “d
- Device protection through pressurised enclosure “p
- Device protection by increased safety “e
- Device protection through intrinsic safety “i
- and many more
The requirements for devices with the respective type of protection are all described in the DIN EN 60079 series of standards. Using the example of our OLLI mentioned at the beginning, we want to explain the two types of ignition protection, flameproof enclosure “d” and intrinsic safety “i”.
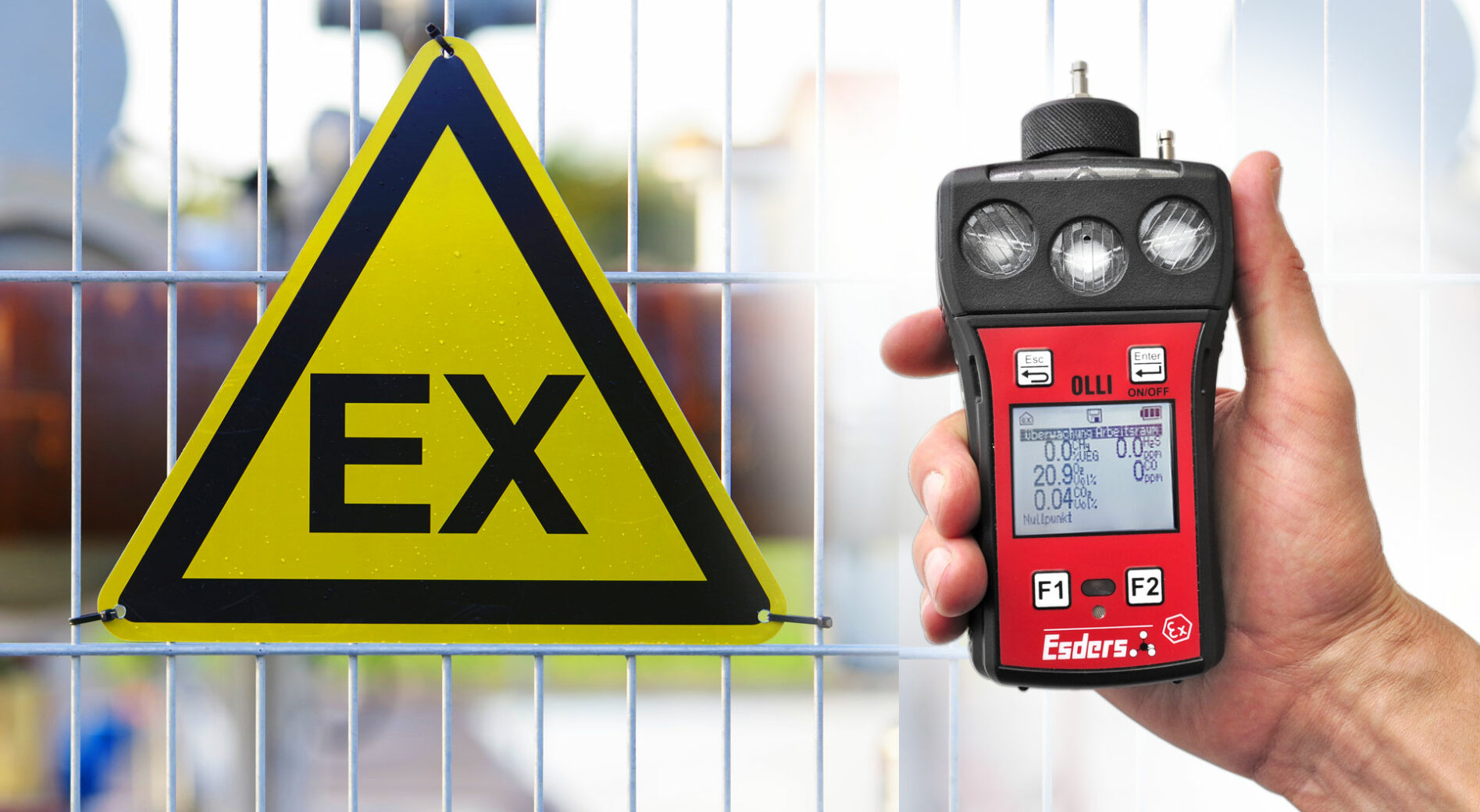
Flameproof Enclosure
For flameproof enclosure “d”, the maximum safety gap described above applies. The sensors installed in gas detection and gas warning devices all have their own type of ignition protection and thus marking, which is or can be independent of the type of ignition protection and marking of the measuring device. The sensors used in the OLLI are either flameproof encapsulated by themselves or are wired intrinsically safe.
Intrinsic Safety
A main criterion for assessing the intrinsic safety “i” of a gas detection & warning device is the minimum ignition energy, which has also been addressed. This means that the energy storage units in the device (e.g. capacities, inductances) must not exceed certain limit values. Since the minimum ignition energy is reduced when hydrogen is added to natural gas compared to normal natural gas, the requirements for the equipment with a higher ignition protection class or explosion group (IIA, IIB or IIC) increase at the same time. Likewise, the requirements for the electrostatic properties of the housing surface of the measuring device are increasing.
Due to the comparability of maximum safety gap and minimum ignition energy or minimum ignition current with regard to the classification of natural gas-hydrogen mixtures into the explosion groups mentioned at the beginning, it can also be stated here that measuring instruments with an IIB certification may be used with a planned addition of 30% hydrogen to the natural gas.
Please note that with this information we would like to provide support for the assessment of a suitable gas warning device. Ultimately, the operator must assess within the framework of his risk assessment which hazards to life and limb are to be expected and select suitable devices accordingly.
We will be happy to provide you with further consultation. You are welcome to download our ATEX overview of all directives and standards for gas detectors. To do this, simply fill in the form below.