Table of Contents
In the first blog post in the series Changes W 400-2, we dealt with the new requirements for personnel and measurement technology. In this blog post, we show what changes there are specifically for the different pressure test methods.
Accelerated Standard Procedure (ASP)
The accelerated standard procedure is an internal pressure test for pipes made of ductile (expandable) cast iron and steel up to DN600 with cement mortar lining. This procedure takes into account that the cement mortar lining of the pipeline is only partially saturated. In the standard procedure, for example, complete saturation is aimed for. The accelerated standard procedure is intended for “small” pipelines in order to limit the time required for the test.
The accelerated standard procedure received extensive changes with the update of the worksheet in order to eliminate problems in practical implementation and to avoid erroneous results.
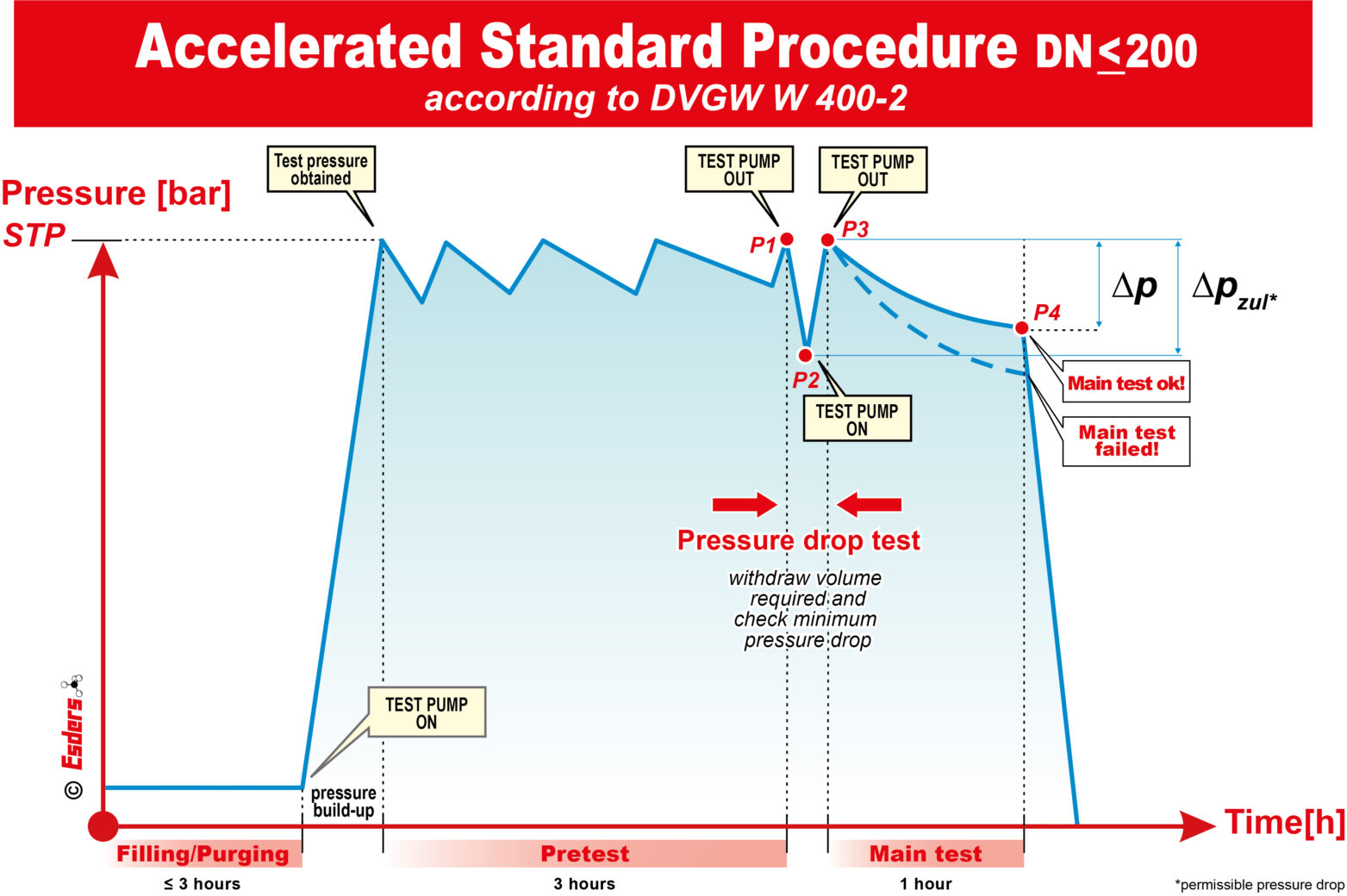
In practice, the 30-minute saturation phase from the previous specifications of the worksheet has proven to be too short, so that in future a 3-hour saturation phase will be used.
Based on the assumption that large pipelines require relatively more time to reach a comparable degree of saturation as small pipelines, several process variants were created in the new worksheet, which are to be selected depending on the nominal diameter of the pipeline.
ASP for DN<= 200 Pipelines with small nominal diameters are tested in the “usual” sequence of the accelerated standard procedure with a modified duration of the saturation phase of 3 hours.
For unforeseen time delays of this procedure (e.g. at the end of the working day or if the pressure drop test failed), the test may be continued in an adapted procedure. Even in the case of a failed main test, the test may be continued or repeated once in the adapted procedure.
Adapted Procedure ASP for DN<=200
If a test interrupted for lack of time needs to be continued or if the main test/pressure drop test has failed, the adapted procedure of the updated worksheet shall be carried out.
The adapted procedure includes the following steps:
- Repressurise to test pressure STP
- Resting phase over 12-18 h without pumping
- Re-pressurisation to test pressure STP
- Pressure maintenance at STP for 30 minutes
- Pressure drop test
- Main test for 60 minutes
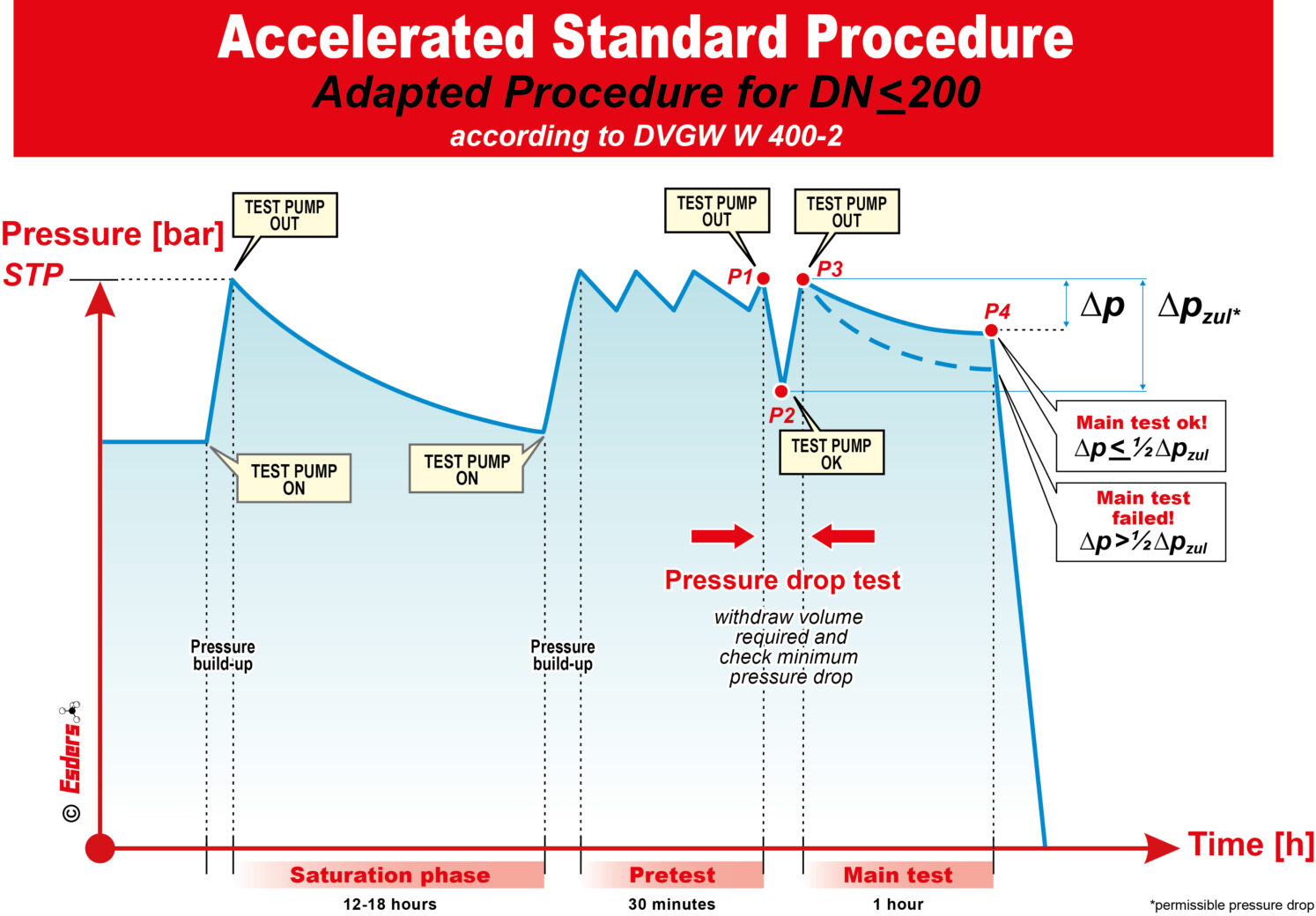
The permissible pressure drop during the main test is determined by the pressure drop in the pressure drop test.
When carrying out the adapted procedure, however, only half of the pressure drop determined in the pressure drop test is permissible!
ASP for 200 < DN <= 600
For larger pipelines it is assumed that partial saturation usually occurs after a longer time than for pipelines with DN < 200. Therefore, the accelerated standard procedure for pipelines with 200 < DN <= 600 has been revised in the updated worksheet. The new procedure includes an extended preliminary test (rest phase), so that usually 2 working days are required.
The procedure includes the following steps:
- Pressure build-up to test pressure
- Pressure maintenance at STP for 60 minutes
- Resting phase for 12-18 hours without pumping
- Renewed pressure build-up on STP
- Pressure maintenance STP for 30 minutes
- Pressure drop test
- Main test for 60 minutes
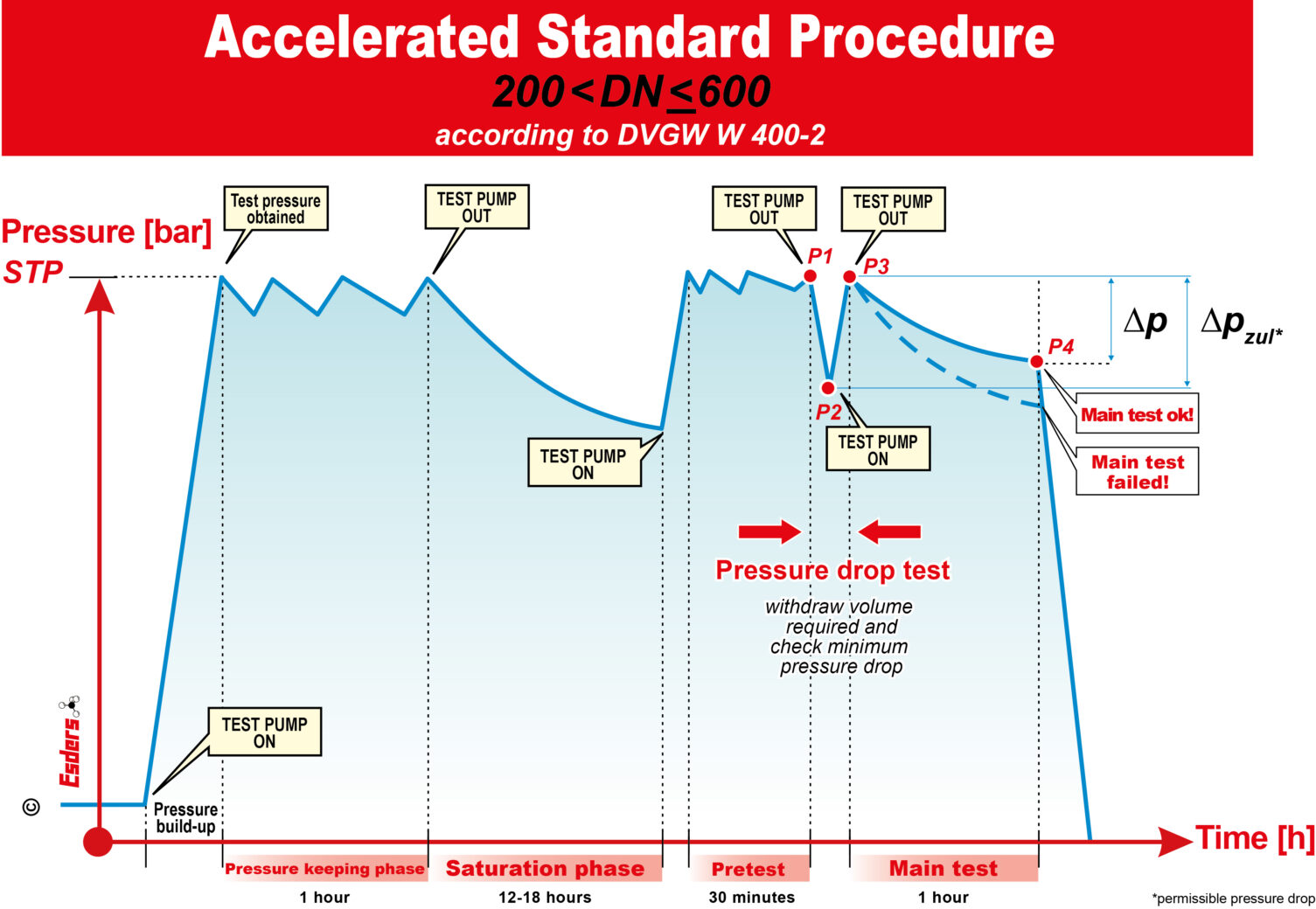
The permissible pressure drop (Δp zul) during the main test is determined by the pressure drop in the pressure drop test.
Subscribe to our newsletter and stay informed
If you would like to be kept up to date with changes to regulations, new products, news on the blog and much more, please fill in the form below.
Contraction Procedure
The contraction procedure is a pressure test method that was developed explicitly for plastic pipelines. Due to the elasticity of the material, plastic pipelines react to pressure in a different way than pipelines made of rigid materials (steel, cast iron). First and foremost, plastic pipes expand under pressure or the material begins to flow. The contraction process is based on a sudden interruption of this flow process through a spontaneous, targeted pressure reduction. This is followed by a contraction of the pipe, i.e. the material contracts again. The resulting pressure increase marks the beginning of the main test. This behaviour is characteristic and easily comparable for many plastic pipes, so that a pressure drop as a result of a leak can be detected in the following main test.
In the contraction procedure, some changes were also introduced with the publication of the updated worksheet W 400-2. In addition to specifications for certain pipe materials, a new limit value was introduced (preliminary test) and another limit value was weakened (main test).
Up to now, a pressure test of PVC pipes was permitted using the contraction method. However, it has been shown in practice that the characteristic viscoelastic behaviour of PE pipes is different from the behaviour of PVC pipes. Thus, the contraction method (as it is currently defined) is not applicable to PVC pipes without further ado with regard to the limit values.
With the publication of the updated worksheet, PVC pipes may only be tested using the standard procedure.
Pipes made of PE 100 SDR17 were previously tested at a test pressure of STP=12 bar. In future, this special procedure will no longer apply, so that pipes made of PE 100 SDR17 will also be tested at 15 bar.
In the updated worksheet of W 400-2, some measures have been taken to ensure that the pipeline is sufficiently free of air during the pressure test. For this purpose, a new limit value has been introduced in the contraction procedure. A minimum pressure drop must occur during the preliminary test. If the pressure does not drop by at least 10% during the preliminary test, it is assumed that there is too much air in the pipeline. If either the 10% condition of the pre-test or the subsequent pressure drop test fails, the purging procedure must be repeated.
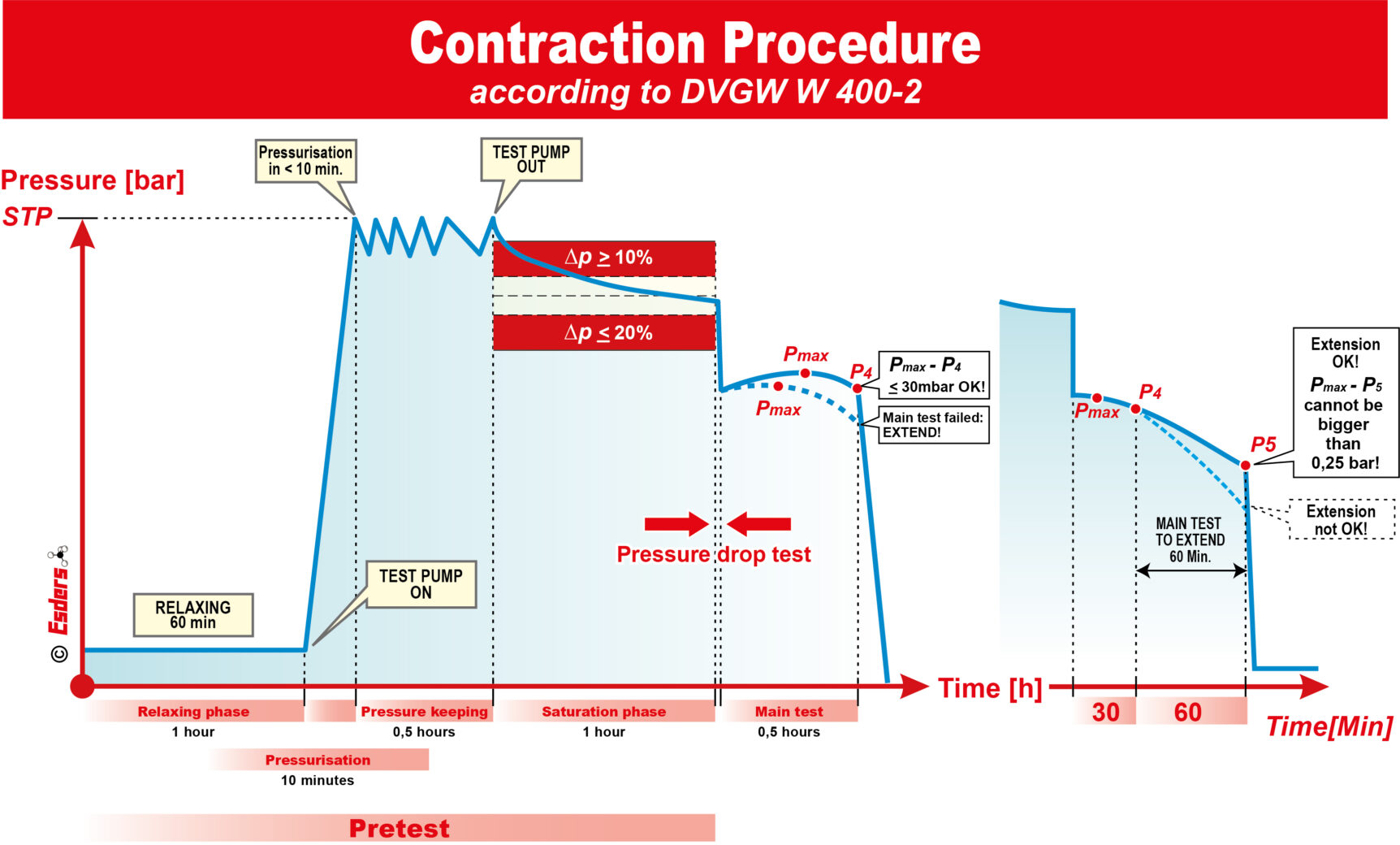
During the main test, the pipeline goes into contraction, which creates a pressure increase. This contraction is usually completed after a duration of approx. 30 minutes, but can also be completed after e.g. 28 minutes. The exact value is highly dependent on current, external conditions and individual properties of the piping system. However, if the contraction of a tight pipeline is completed early (e.g. after 28-29 minutes) and a slight pressure drop inevitably occurs, this would lead to an extension of the main test according to the “old” regulations. In order to take this into account and to prevent “unnecessary” extensions of main tests, a permissible pressure drop of 30 mbar was introduced for the main test.
Influence-Minimised Standard Procedure
The influence-minimised standard procedure is a pressure test procedure for cast iron and steel pipes with cement mortar lining. It was published several years ago and has been available in the smart memo since its introduction. With the update of the worksheet, it was added as an independent procedure. From a technical and time point of view, the procedure is located between the accelerated standard procedure and the standard procedure. The saturation of the cement mortar lining of the pipeline is usually advanced, but not complete (as in the standard procedure). Thus, preliminary tests in the influence-minimised standard procedure for pipelines with cement mortar lining take a maximum of 24 hours, in the standard procedure at least (usually significantly longer than) 24 hours.
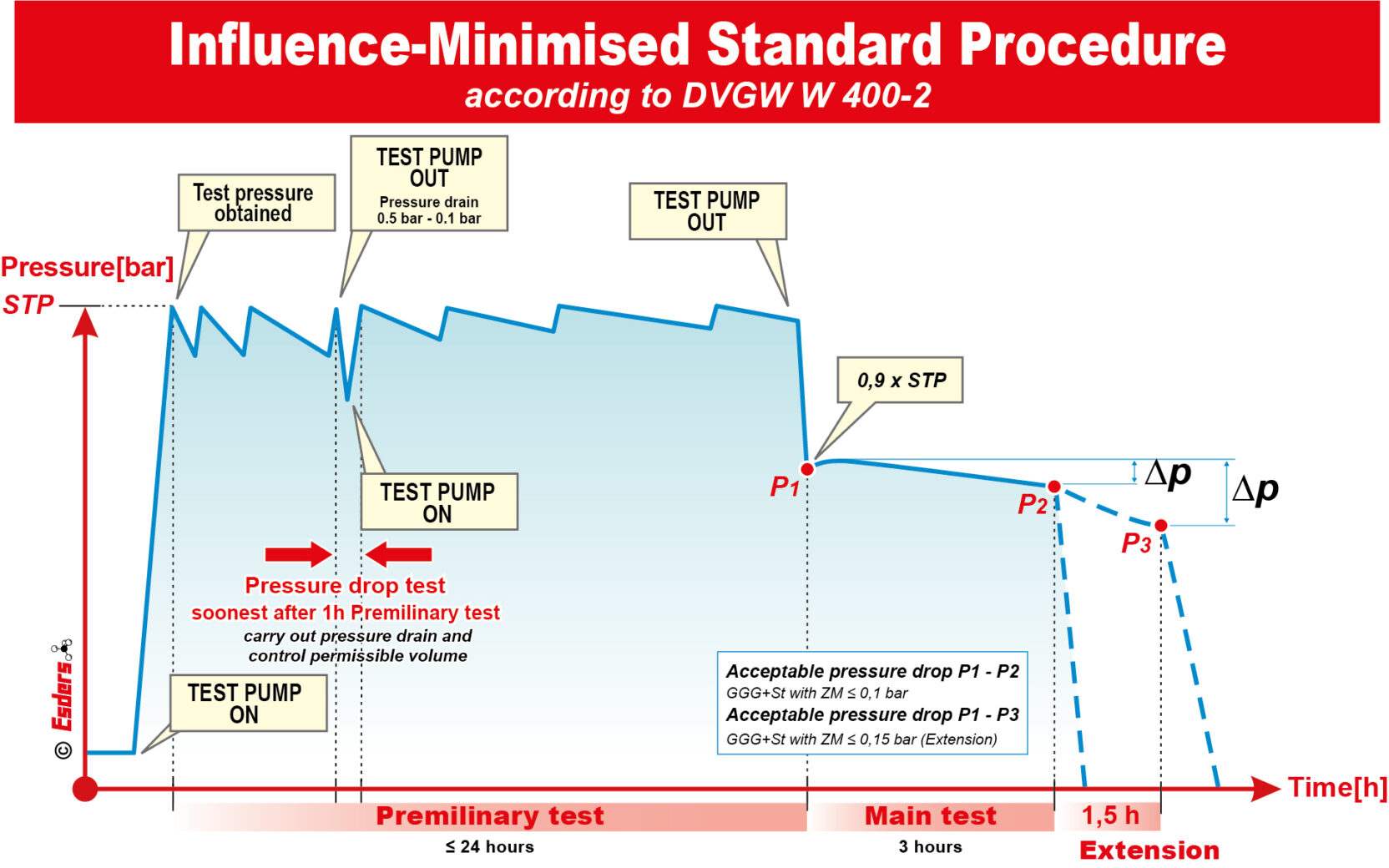
The details of this procedure have already been described in the blog post The basics of pressure tests on water pipelines – pressure loss method according to W 400-2. There are no changes to the current worksheet publication.
Standard Procedure
The standard procedure can be used for all pipelines and all materials. The time required is the greatest compared to the other procedures, which is particularly noticeable for pipelines with cement mortar linings. Here, the cement mortar lining must be completely saturated so that it has no influence on the final main test.
The standard procedure remains fundamentally the same with the update of the worksheet. However, some details have been changed.
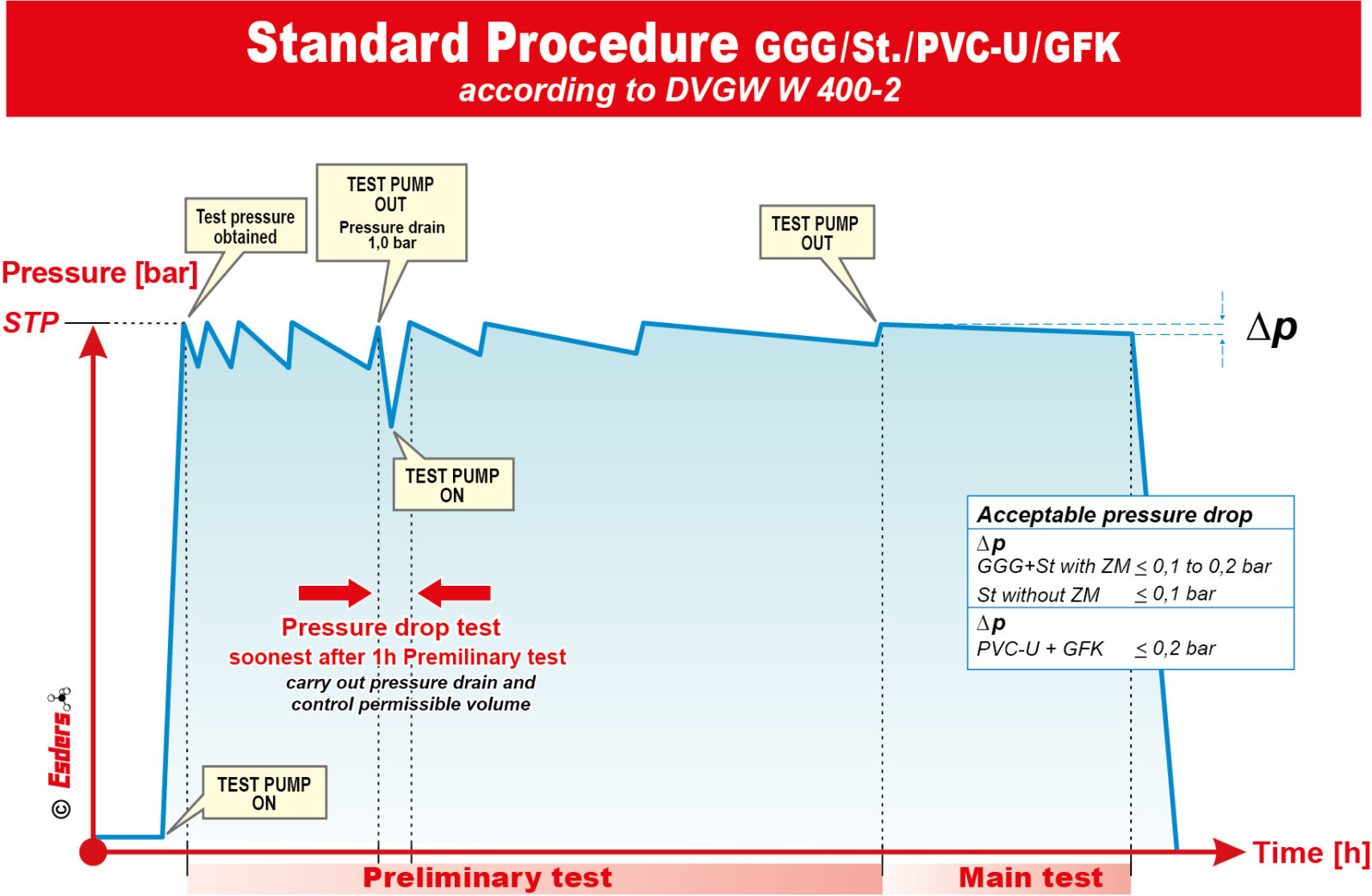
The standard procedure is also subject to the new requirement that pipelines made of PE 100 SDR 17 are to be tested with STP=15 bar in future.
The pressure reduction to be carried out in the pressure drop test must always be 1 bar in future with the update of the regulations. The alternative pressure reduction of 0.5 bar is no longer applicable.
In addition, the update contains another novelty especially for pipelines made of Pe100/PE80/PE-Xa. If the main test for pipelines made of these materials fails, it may be repeated one more time. In this case, the test pressure STP should be restored once and then the pressure checked for the specified duration of the main test.
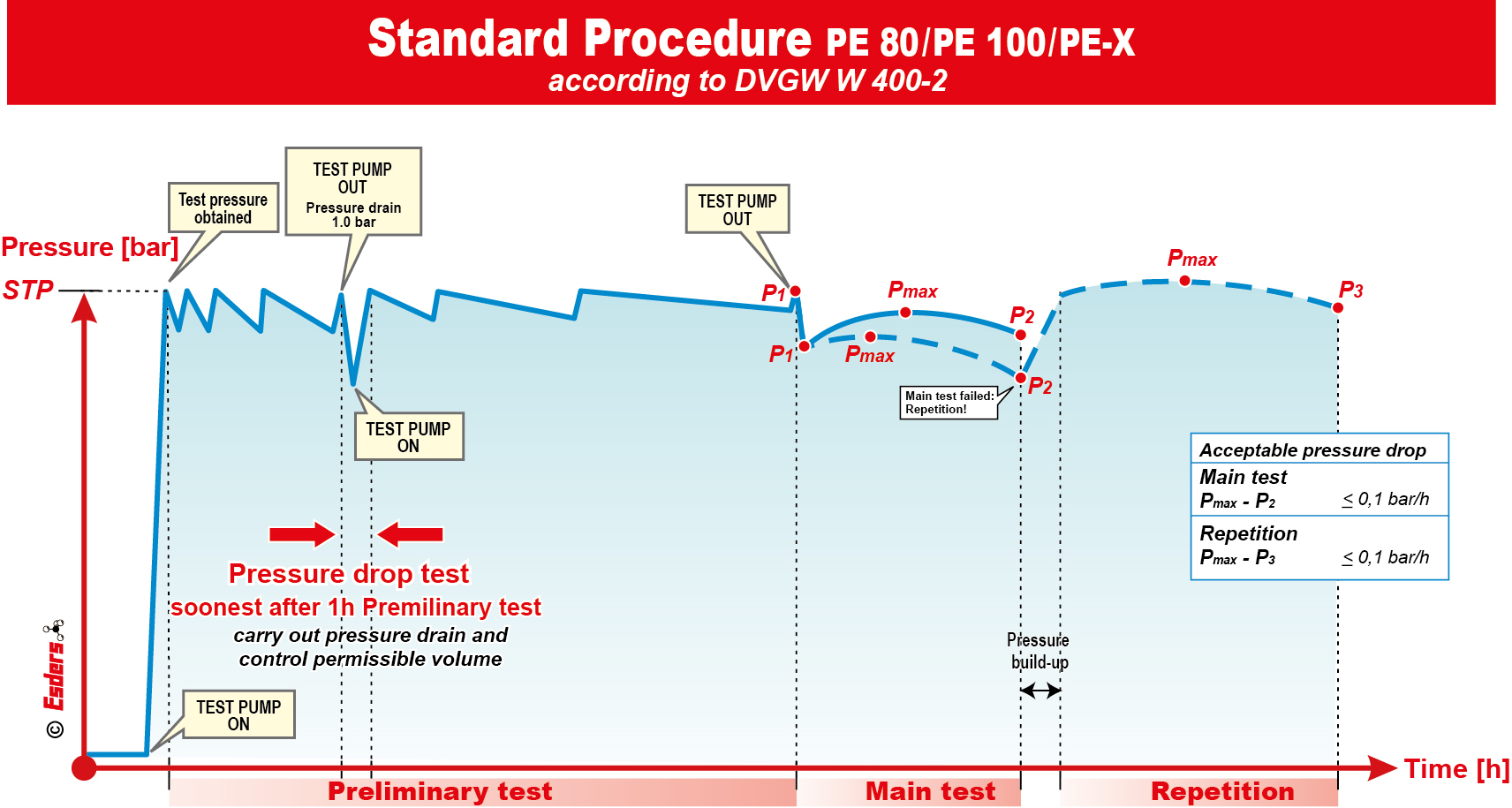
Since it can be assumed that pipelines with cement mortar lining cannot reach the complete saturation required for the standard procedure within 24 hours, the duration of the preliminary test was formally set to at least 24 hours. Typically, it should last much longer.
Pressure tests according to W 400-2 with the smart memo
All these procedures can be easily performed with our electronic pressure test case smart memo and the option DVGW W 400-2. The smart memo guides you through the test in an automated sequence, displays measurements and progress, and stores and documents all relevant test data. You can read more information about how the procedure is carried out in our blog post here.
Still have questions?
You have now gained a deeper insight into the various procedures according to W 400-2. It is clear that this testing requires a lot of technical know-how and precision. At Esders, we pride ourselves on having this expertise and making it available to our customers. We are ready to assist you with your pressure measurement challenges and ensure that your systems meet the highest standards.
Don’t hesitate to contact our technicians to learn more about our products. We will get back to you in a timely manner!