In Germany, water pipelines in the drinking water supply sector must be subjected to a pressure test before they are put into operation in order to prove that the construction work has been carried out properly and that the pipeline system is leak-proof. Requirements for the procedures and guidelines for carrying them out are set in worksheet W 400-2 of the DVGW (German Association of the Gas and Water Industry). These are complex procedures with many different details that depend on the test procedure and material selected. The menu-guided test sequences in the smart memo can be used to carry out these tests. All test sequences in the device are programmed according to the current version of the regulations and support the user in carrying out the pressure test properly.
For more information on the new requirements and changes due to the update of the regulations (status 08/2022), please read our blog post W 400-2.
The applications chapter will deal more specifically with the testing process and technology of the equipment required for this.
Tests according to W 400-2
Each procedure basically includes three phases: pre-test, pressure drop test and main test.
The main test is the final phase of a procedure and is used as the final evaluation of the tightness. Over the duration of the main test, the pressure drop in the pipeline is determined and compared with a permissible pressure drop. The specifications for test duration and permissible pressure drop differ significantly in the individual procedures and depending on the pipeline to be tested. A pressure sensor with a regulation-compliant measuring range and sufficient accuracy is required to measure the pressure curve.
The pressure drop test is carried out in every procedure following the pre-test and before the main test. It is intended to check that the pipeline system is free of air. An excessive amount of residual air in a pipeline during a hydrostatic test will significantly influence the result of the main test.
In the current W 400-2 regulations, there are strict requirements for the performance and evaluation of the pressure drop test. The drained water volume must be determined with a digital measuring device and the measured value must be transmitted to the pressure testing device used.
The pre-test has the greatest distinctions between the individual procedures, as it is intended to bring about different conditions depending on the pipeline material. During the pre-test of the contraction method, plastic pipelines expand under test pressure. In the pre-test of the accelerated standard procedure, a cement mortar lining (CML) of a steel/cast iron pipeline is to be partially saturated with water under test pressure, whereas in the standard procedure the CML must be fully saturated. The procedures are therefore complex and involve many different details depending on the type of procedure, the pipe material and the pipe size. More information about the procedures can be found in our blog post.
High-quality measurement technology that conforms to the regulations should be used to carry out the procedures. The components required for carrying out the procedures are listed below. All procedures according to W 400-2 can be carried out with this equipment.
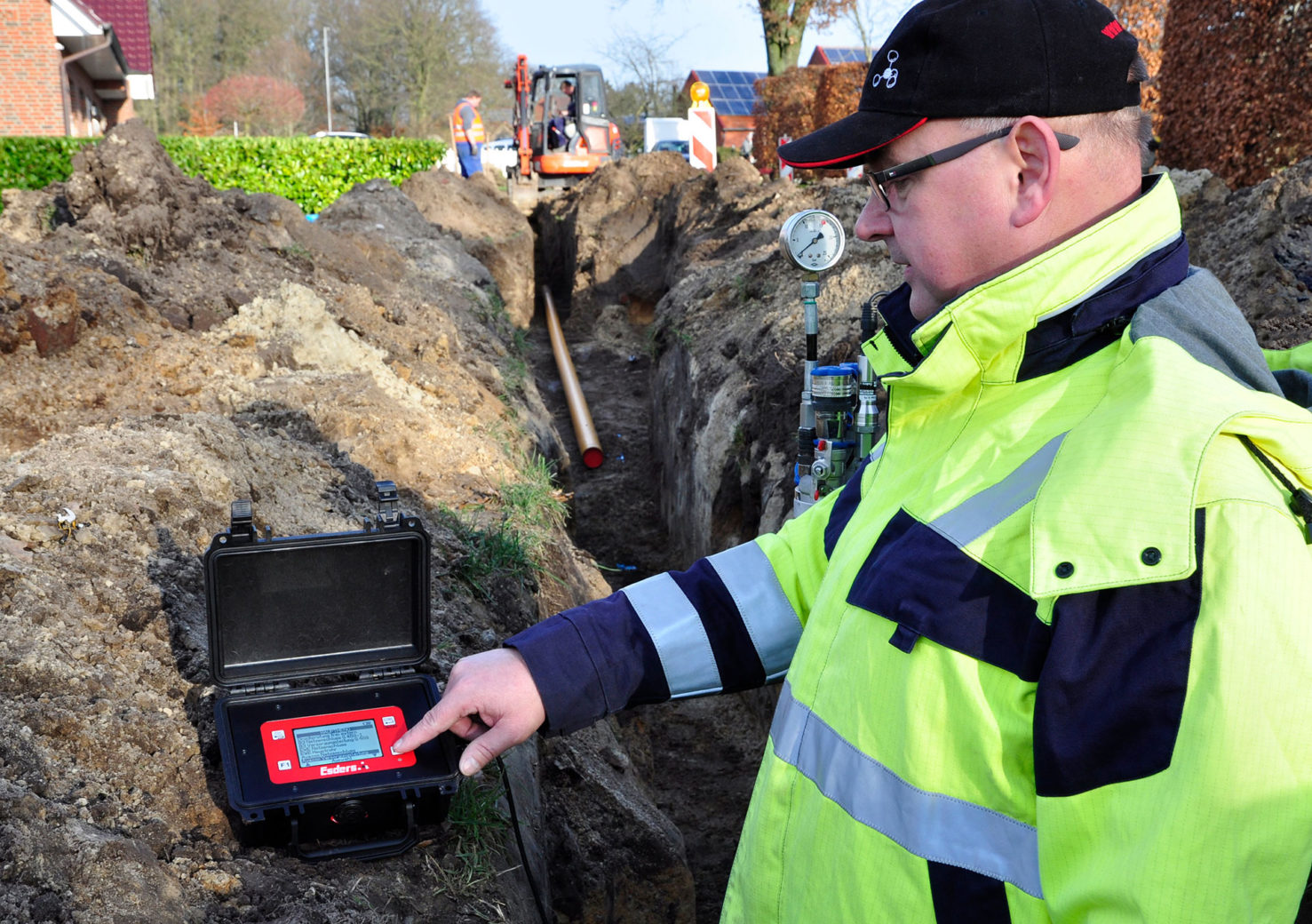
Equipment
smart memo
A smart memo with the DVGW W 400-2 option enabled is required to perform this test. The smart memo guides you through the test in an automated sequence, displays measurement data and progressions, and stores and documents all relevant test data. To use the remote control option for the MPP 30-30 and the air volume determination in the pressure build-up phase of a test, the smart MPP option is also required. Further information on remote control and air volume determination can be found further down in the text. The LTE-GPS option can be used for digital transmission of the test results to the Esders Connect portal (in order to create paperless documentation). This allows data to be sent directly from the device. Suitable external sensors EDS2 are required for measurement data acquisition for the test.
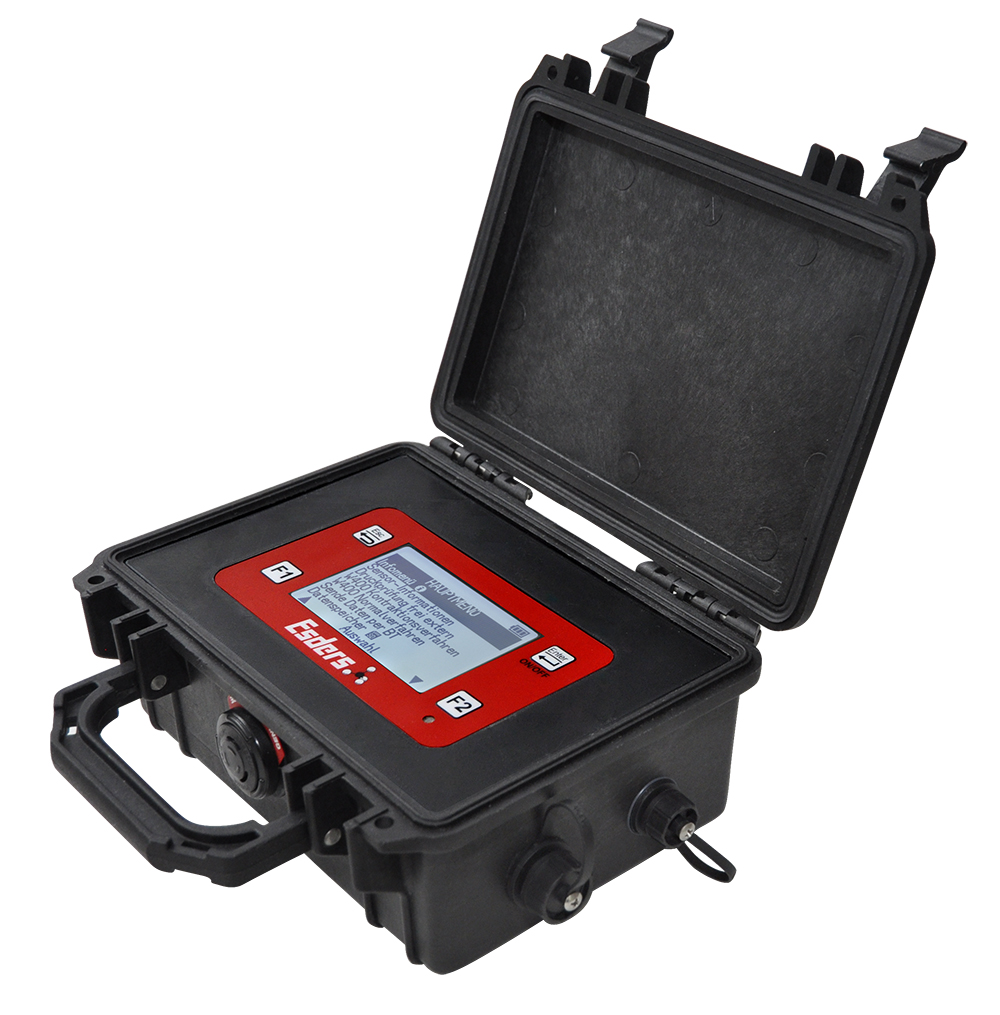
External sensors
Several external sensors can be connected to the smart memo at the same time. Depending on the requirements from the regulations, sensors with a suitable measuring range and accuracy can be selected from the Esders range and connected to the smart memo.
Pressure sensor EDS2-P
The EDS2-P 25 bar 0.1% pressure sensor is suitable for the test. The resolution of the measured value in the smart memo is 10 mbar.
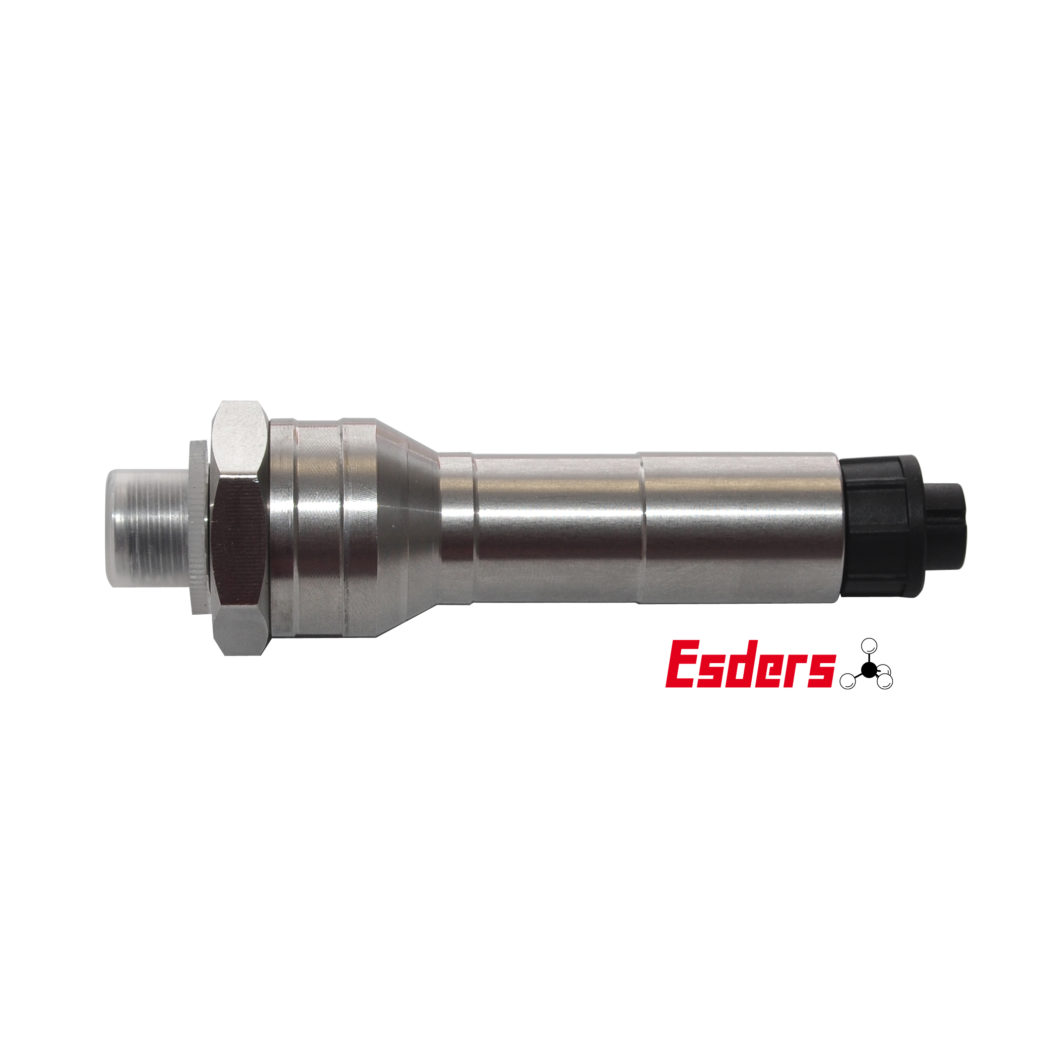
Flow sensor/flow meter EDS2-V
Since the new publication of regulation W 400-2 (08/2022), an additional sensor that measures the amount of drained water is required to carry out the pressure relief test in accordance with the regulations. For this purpose, the external EDS2-V sensors can be connected to the smart memo. For the majority of tests, the EDS2-V 1-42 l/min is suitable. Normal water quantities can be recorded with this sensor. For very large discharge quantities, there is the alternative EDS2-V 4-160 l/min.
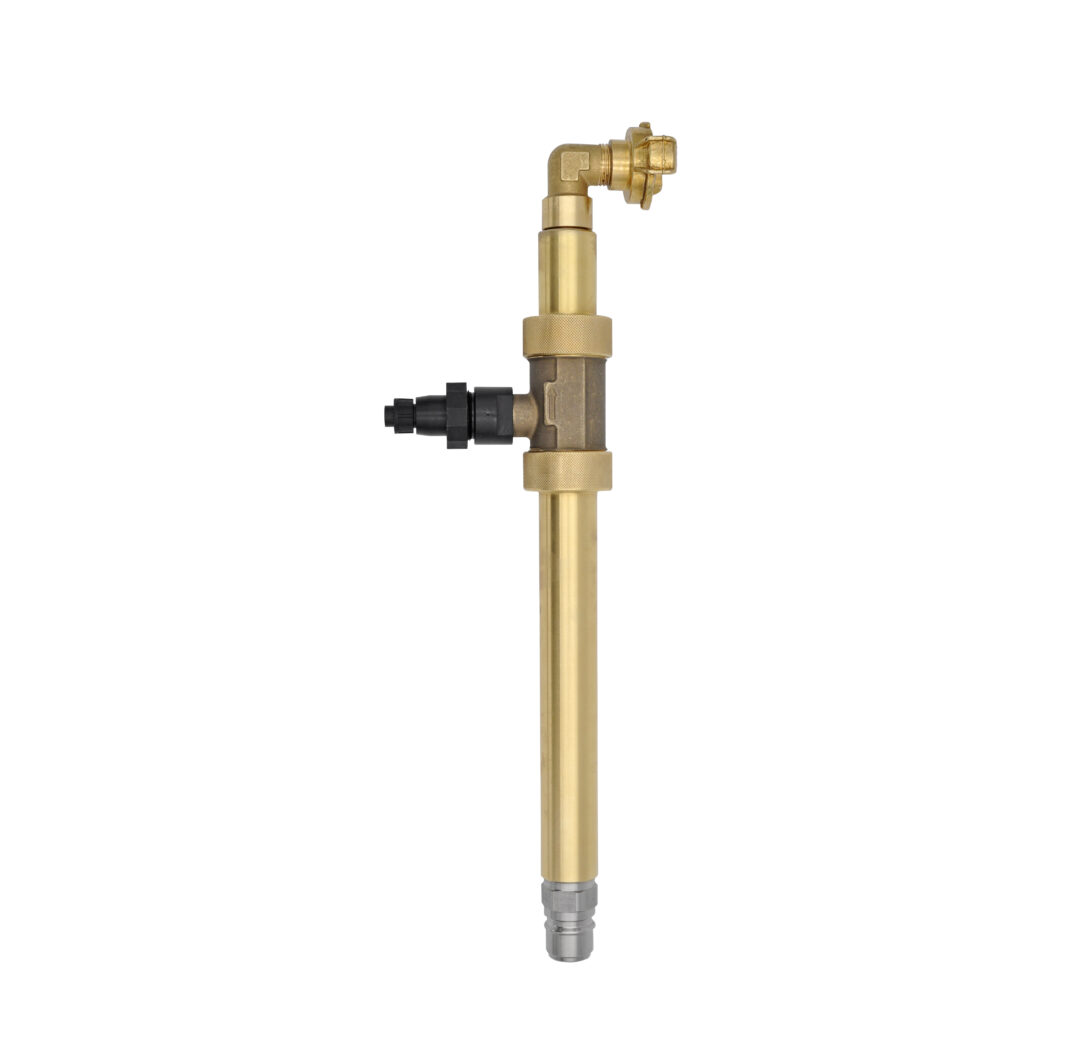
Temperature sensor EDS2-T
An external temperature sensor EDS2-T can be used to measure and document the pipeline temperature. Since the new publication of the W 400-2 regulations (08/2022), at least one representative measurement per phase of the process is required. The requirements for measuring range and accuracy from W 400-2 are met by the following temperature sensors: EDS2-T ground stake 0.1K and EDS2 contact sensor 0.1K.
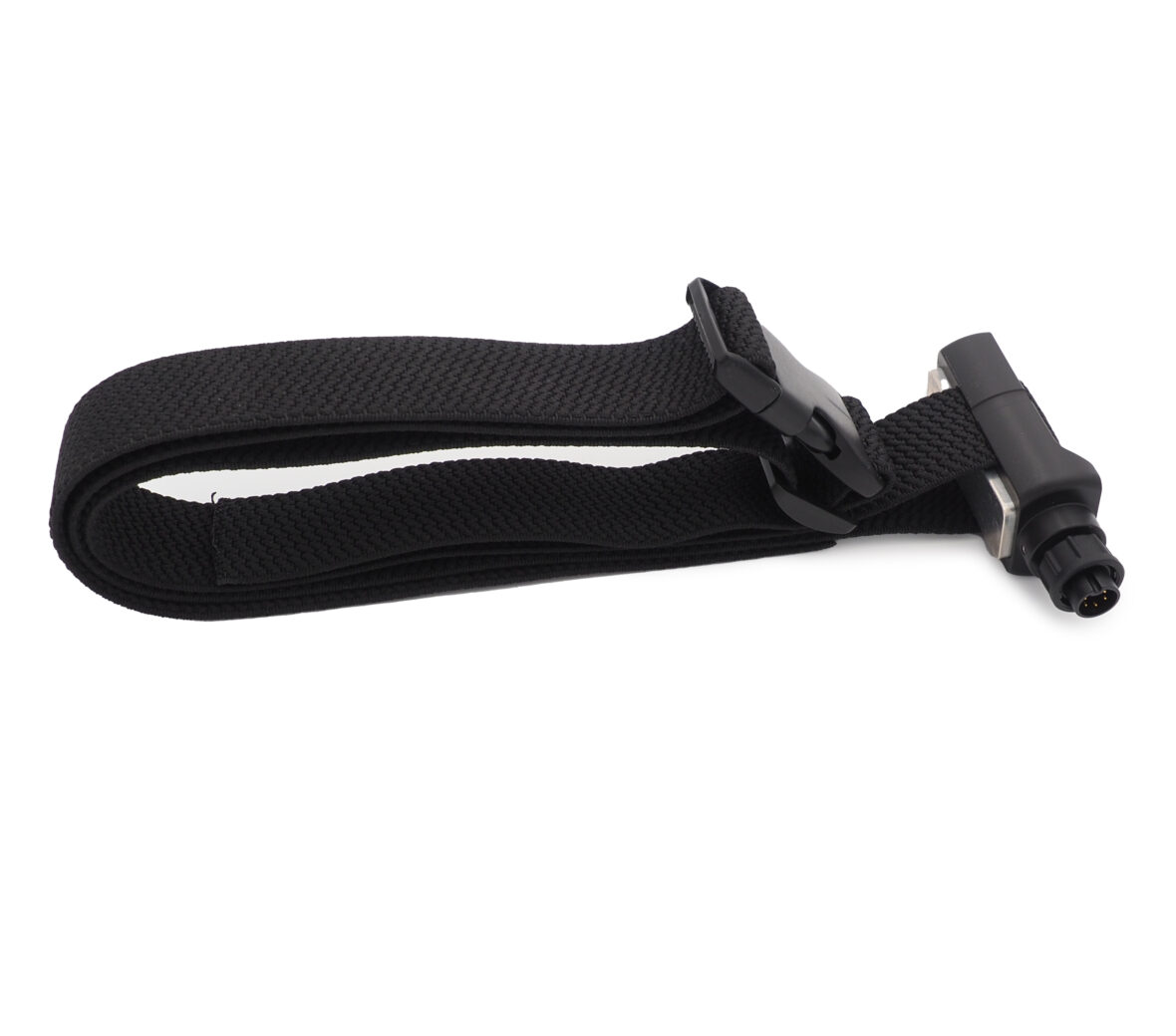
Accessories for connecting external sensors
To connect a sensor to the smart memo, one connection cable B11 is required for each sensor. To connect several sensors to the smart memo, one T-connector B11 must be used per additional sensor. Since in most cases there is only a small distance between the pressure sensor and the contact sensor and between the pressure sensor and the EDS2-V, we recommend a connection cable B11 1 meter for these connections. For all other connections, we recommend connection cable B11 5 meters.
Test pump MPP
Motor test pumps should be used to build up pressure in the pipeline to be tested. These devices ensure an exact start-up of the selected test pressure and keep the test pressure within the required tolerance limits.
All motor test pumps from Esders GmbH operate in accordance with the regulations and can be used to carry out the test procedures.
When performing a contraction procedure, the delivery capacity of the motor test pump shall be such that the pressure build-up to test pressure is completed within 10 minutes.
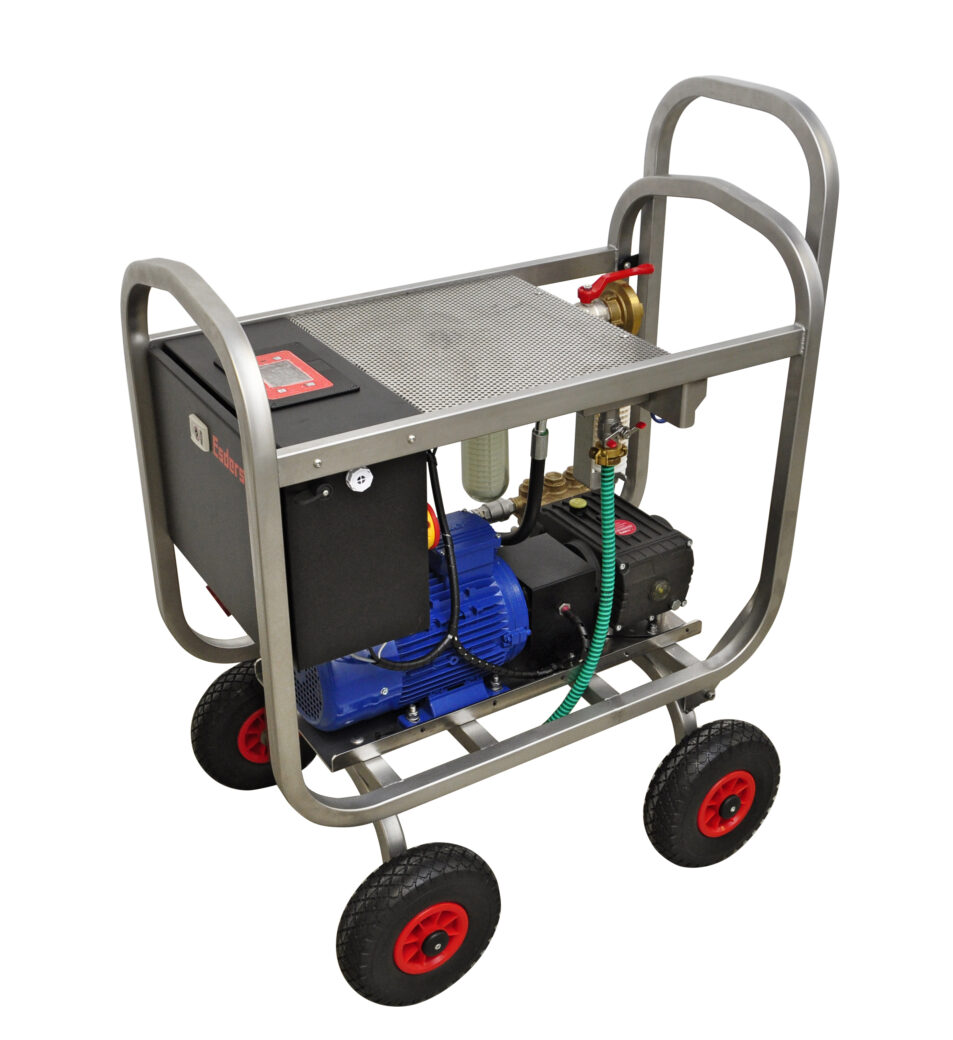
When using the MPP 30-30 test pump in combination with the smart memo, the additional functions of air volume determination and remote control can be used, which are activated by the smart MPP option in the smart memo. The air volume determination provides a result about the residual air in the pipeline, which must not exceed a certain limit value according to the W 400-2 regulations. The test procedure provides for a determination of the residual air via the pressure drop test, which, however, takes place much later in the procedure than the air volume determination by the smart memo. With the smart memo and the MPP 30-30, it is evaluated directly after the pressure build-up phase at the beginning of the test whether there is too much air in the pipeline. In addition, the remote control for the MPP 30-30 can be activated so that the smart memo controls the MPP 30-30 and the test can be automated as much as possible.
The MPP 30-30/smart memo connection cable is required to establish communication between the MPP 30-30 and the smart memo. A suitable pressure hose must be used to generate the test pressure in the test pipeline.
To activate the air volume determination, the flow measurement option in the MPP 30-30 is also required. With the help of the flow measurement, the amount of water delivered by the pump is measured. These measured values serve as the basis for determining the air volume in the pressure build-up phase.
Test head and standpipe
To carry out the water pressure test, several connections are necessary for different purposes and at different times. A pressure hose must be connected to generate the test pressure. To carry out the pressure drop test, another connection must be available for removing the water volume. Since some procedures require a new pressure build-up after the pressure drop test, separate connections for the pressure hose and the water drain are required. In addition, the test pressure must be measured as close as possible to the test pipeline. A connection for a control pressure gauge is also required for safety reasons.
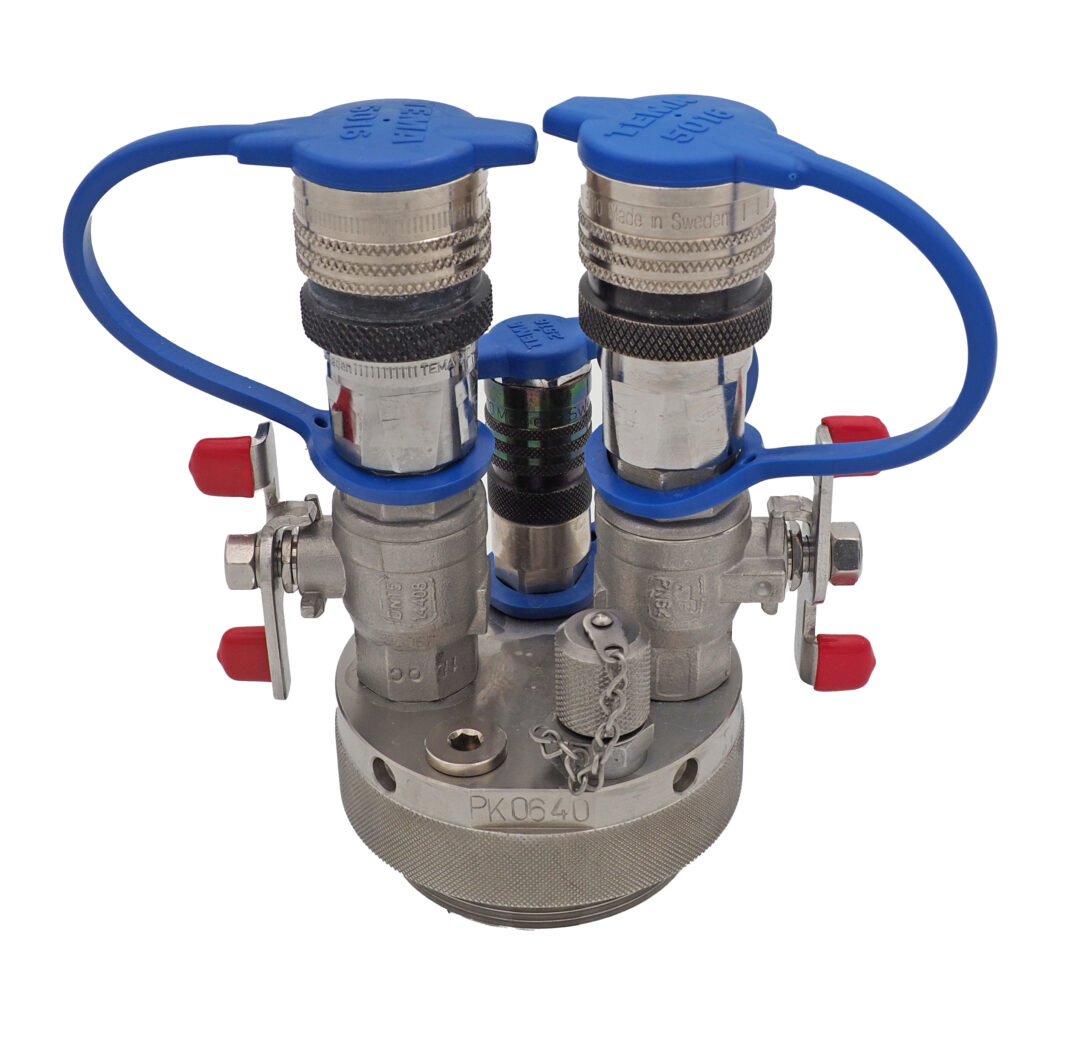
The test head HANS offers these connection options. Two quick couplings series 5000 with integrated ball valve are provided for the connection of the pressure hose and for the connection of the EDS2-V. The pressure sensor can be connected directly to the test head via a screw coupling in order to optimally measure the pressure in the pipeline to be tested. A control pressure gauge can be connected via a small quick coupling series 2500.
To facilitate work, water sampling and optimal filling of the test pipeline, the use of a standpipe is recommended. The test head HANS can simply be screwed onto the standpipe.
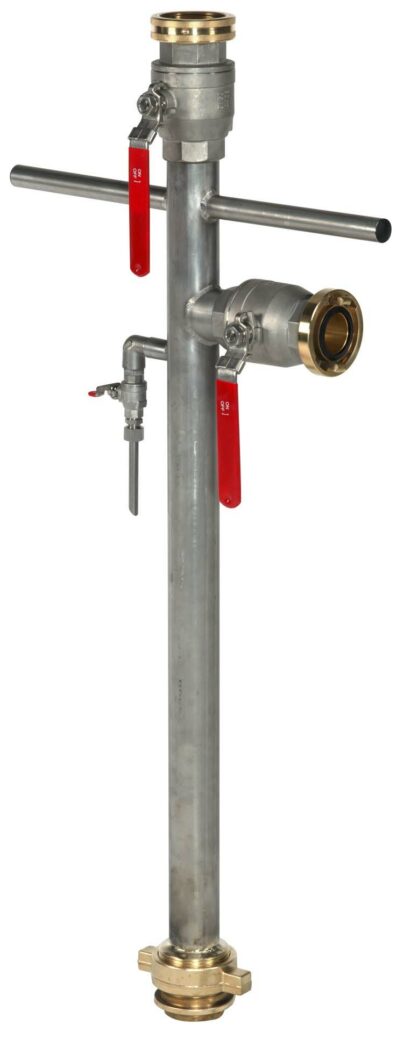
Accessories
If no EDS2-V is used to determine the drain quantity during the pressure drop test or for better control of the water flow (when using the EDS2-V), the drain hose Hyd16 can be used. It can be connected either in the coupling on the HANS or on the outlet side of the EDS2-V.
In order to connect the EDS2-P pressure sensors to the test head, a pressure-resistant adapter 1610N-1/4″ IT is required. It is sealed with an O-ring on the pressure sensor side and via a screw coupling on the test head side.
Device technology and accessories
ATTENTION: You need the connection cable with 5 m length 2x
ATTENTION: You need the T-connection piece 2x
- 1x smart memo (Article 221200)
- 1x Option LTE-GPS (Article 222610)
- 1x DVGW W 400-2 option (Article 222600)
- 1x smart MPP option (Article 222628)
- 1x EDS2-P 25 bar (Article 361012)
- 1x EDS2-V 1-42 l/min (Article 402401)
- 1x EDS2-T ground stake 0.1K (Article 222204)
- 2x Connection cable B11 5 m (Article 227002)
- 1x Connection cable B11 1 m (Article 227220)
- 2x T-piece B11 (Article 227006)
- 1x MPP 30-30 (Article 401005)
- 1x Option flow measurement MPP 30-30 (Article 405832)
- 1x MPP/smart memo connection cable (Article 401100)
- 1x Pressure hose Hyd16 (Article 402011)
- 1x Test head HANS (Article 402066)
- 1x Standpipe hydrant foot (Article 402005)
- 1x Pressure gauge 0 to 25 bar (Article 402050)
- 1x Hose Hyd16 2 m Geka-S5020N (Article 402012)
- 1x Adapter 1610-1/4″IT (Article 222013)
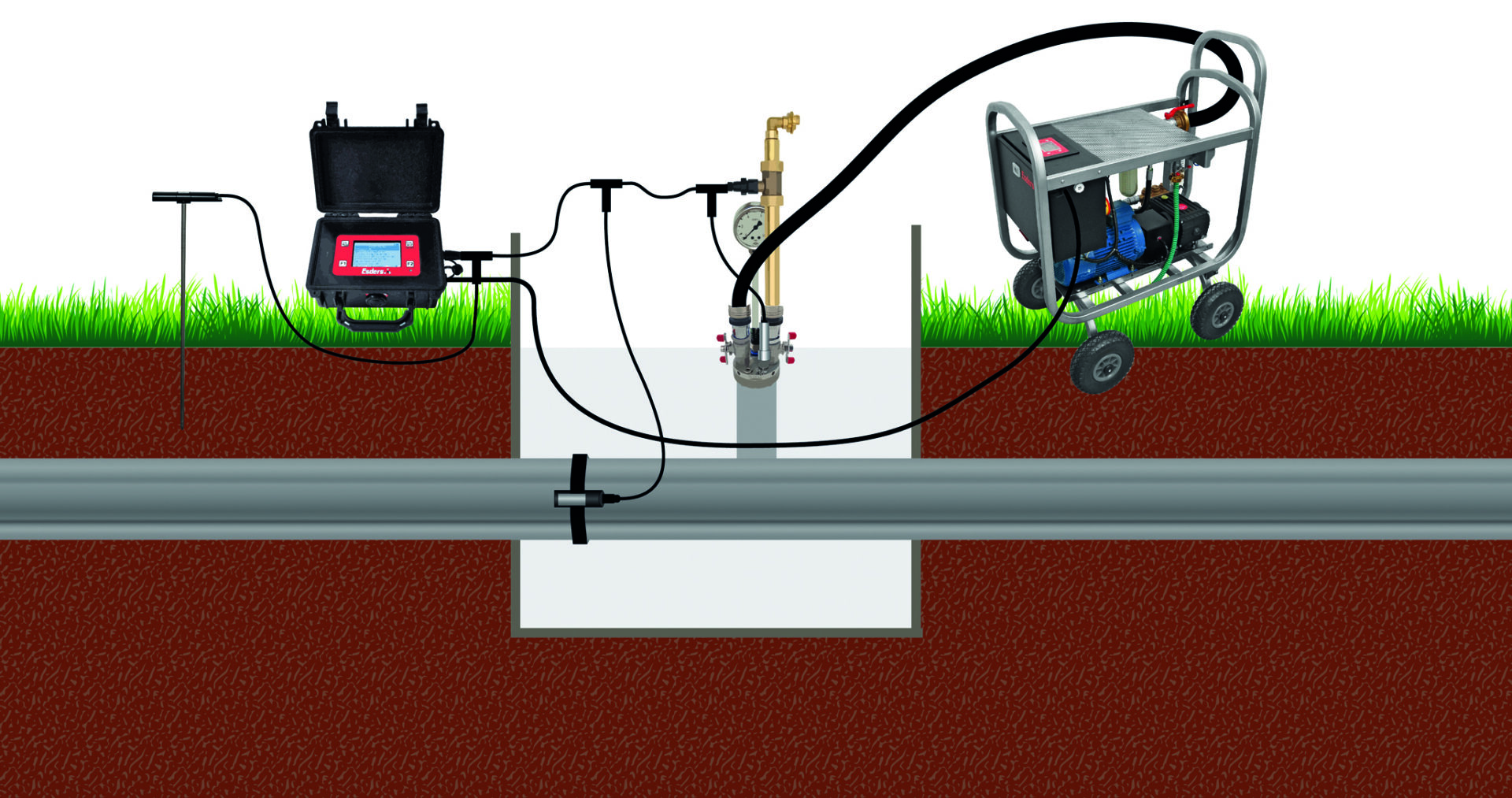