As part of the maintenance or repair of the water, wastewater and district heating network as well as separator systems, the inspection of manholes is one of the tasks of the specialists. As work on and in manholes (often related to Confined Space Entry, CSE) is associated with various hazards, there are some aspects to consider. Depending on the location of a manhole, the local traffic situation must first be taken into account and, if necessary, measures must be taken to divert traffic. The most common hazards when working in a manhole are the danger from substances, which include solids, liquids, vapours and gases, each in quantities and concentrations that are hazardous to health, and the danger of falling. As protection against a fall, a tripod with a height safety device including a rescue lift function is usually set up above the manhole. The person working in the manhole is attached to this by means of safety harnesses and ropes. In this article, we want to specifically address the hazard of dangerous gas concentrations and oxygen deficiency and describe the clearance measurement with our gas detector OLLI.
What is clearance measurement?
In accordance with DGUV rules 113-004 and 103-003, clearance measurement means determining a possible concentration of hazardous substances or the oxygen content before and during work in enclosed spaces with the aim of determining whether the atmosphere in the enclosed space allows safe working. It is thus a measure to protect workers from hazardous substances. Among the gases in the vicinity of manholes, methane (CH4), carbon dioxide (CO2) and hydrogen sulphide (H2S) are the most common hazardous substances, in addition to oxygen (O2) deficiency. Occasionally, carbon monoxide (CO) is also monitored for, as this can be produced in road traffic during incomplete combustion of fuels.
What needs to be considered before the clearance measurement?
A clearance measurement is usually carried out using a suitable gas warning device with certified measurement function for explosion protection, toxic gases and oxygen. The OLLI has these certifications, which were carried out in accordance with the standards DIN EN 60079-29-1, DIN EN 45544 and DIN EN 50104. Before the clearance measurement can take place, the proper function of the gas warning device must be checked by means of a visual inspection and a short bump test. This is required every working day according to DGUV information 213-056 (leaflet T 021) and 213-057 (leaflet T 023). The device including the probe is visually checked for damage and briefly exposed to a suitable test gas to check whether it reacts correctly. The integrated pump is also tested for function. With the OLLI, both can be carried out using the “Bump test” menu item, which can be started from the main menu. We have created a tutorial for this.
In addition to the daily bump test, a functional test of the device must be carried out at least every four months. In addition to the visual inspection, this includes a calibration and, if necessary, adjustment of the sensors of the gas warning device. This procedure can also be carried out directly on the device via the menu item “Calibration/Adjustment”.
All functional tests and bump tests of a gas warning device must be documented. With our Esders Connect portal, we offer digital solutions for paperless and GDPR-compliant documentation and management of all tests.
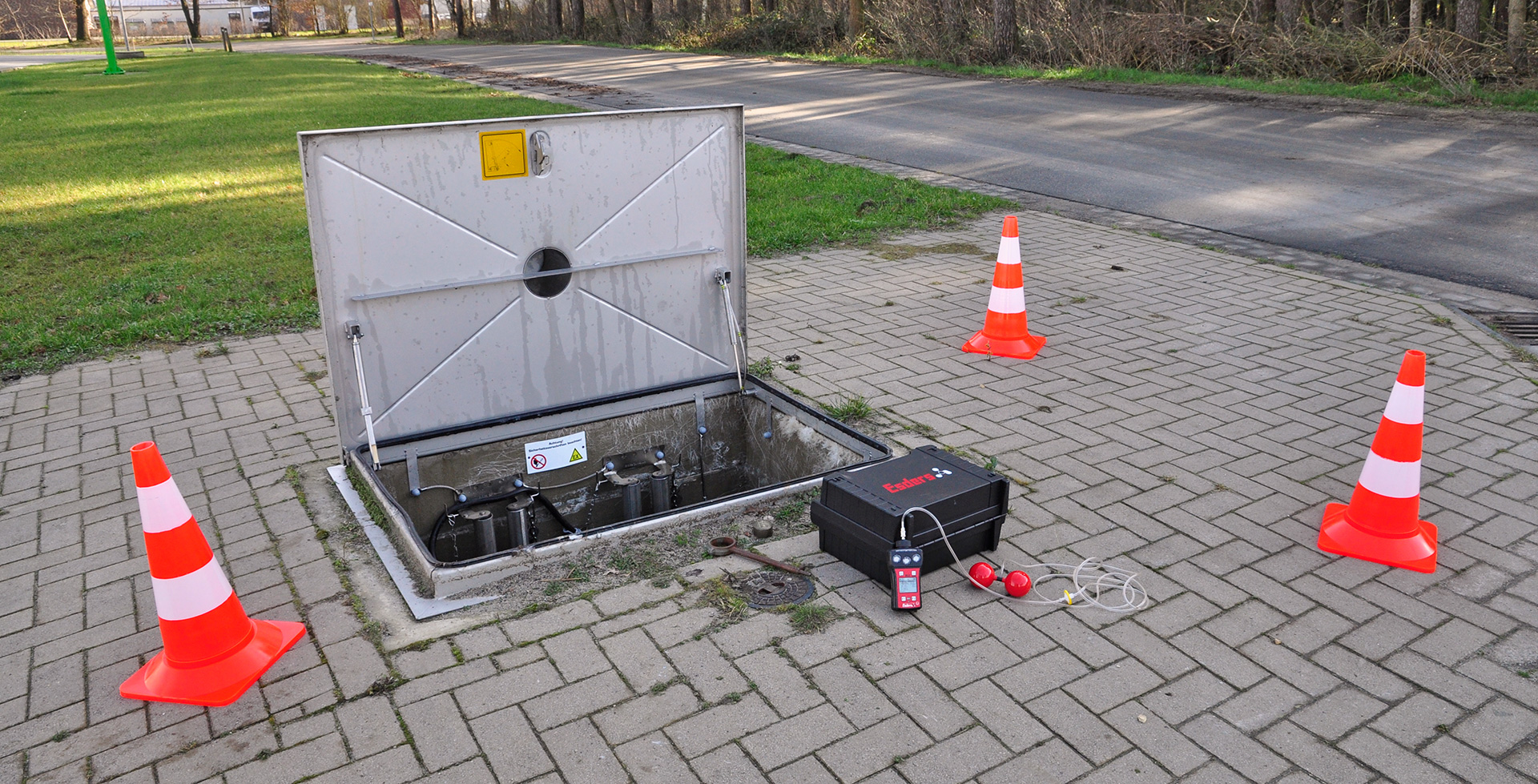
How to carry out the clearance measurement?
If the bump test and visual inspection have been carried out successfully, the clearance measurement is carried out before the work begins, i.e. before climbing into a manhole. Our OLLI is set to “Confined Space Entry” for this purpose and the device is switched on in clean ambient air. After the sensor run-in phase, the OLLI is ready for use and the measurement can be carried out with the floating probe connected.
The ready-to-use status of the OLLI is indicated by an optical and acoustic signal approx. every 10 seconds. During the measuring process, the readings are shown on the display of the OLLI. If the set limit values are exceeded, the device activates an alarm. In this case, entry into the manhole is not permitted and appropriate measures must be taken (e.g. ventilation, use of personal protective equipment, etc.).
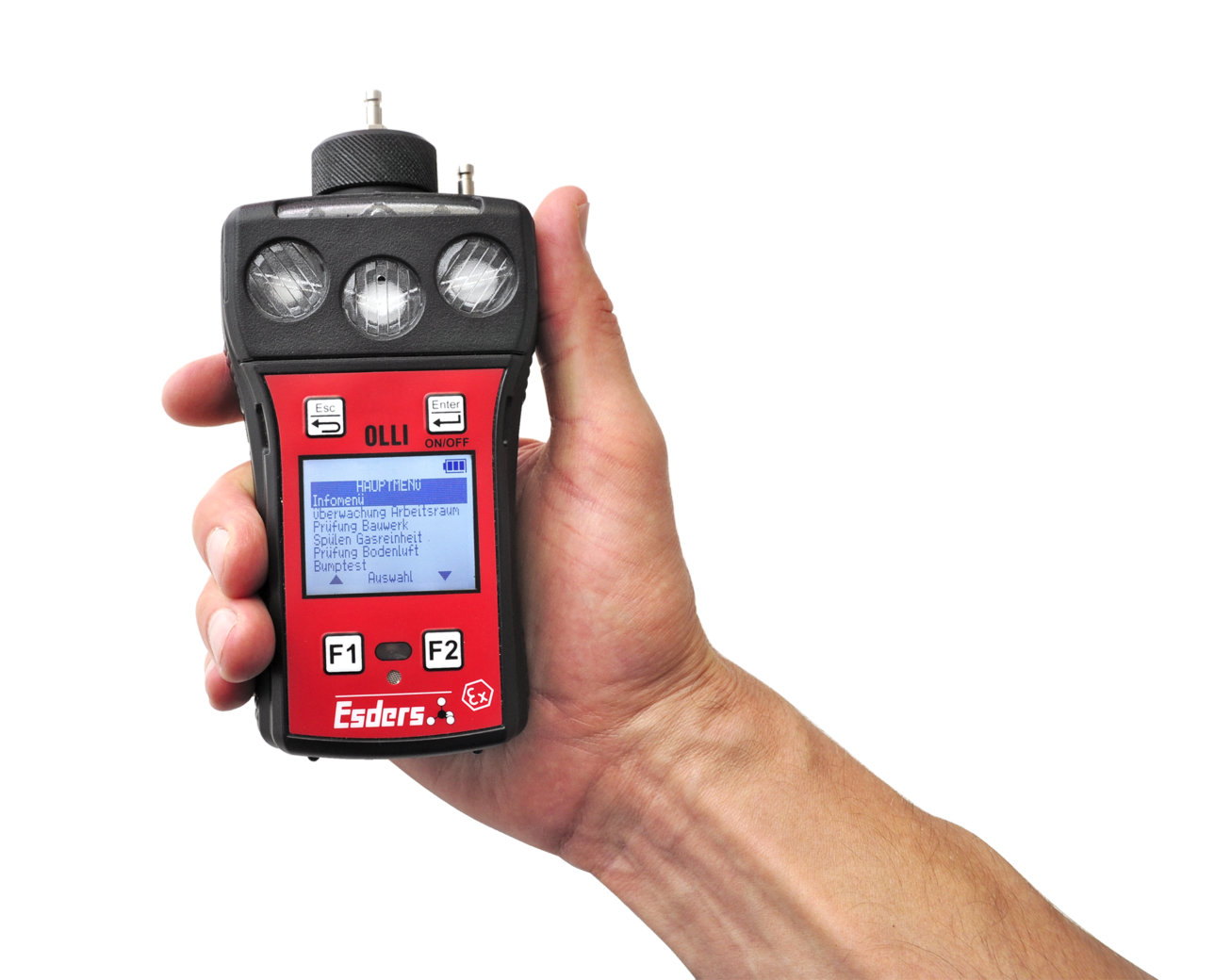
What must be observed after the clearance measurement?
Since the atmosphere in a manhole can change during the work, continuous monitoring of the atmosphere in the manhole is required after the clearance measurement. For this purpose, the person working in the manhole can wear the measuring device directly on his body. Alternatively, a safety worker, who is required for this work and stands outside the manhole, can use the measuring device with the help of a connected floating probe to monitor the atmosphere. This protects the device from contamination in the manhole. The person who takes over the clearance measurement must have been trained as a specialist in accordance with DGUV Principle 313-002. According to this, only persons who have the necessary expertise may be commissioned to measure the clearances. This refers to:
- the measuring devices or measuring methods used,
- the hazardous substances to be measured,
- the operational conditions, e.g. nature of the enclosed spaces; possible installations; possible discharges that may influence the measurement.
Protocol for clearance measurement
We have created a special protocol for clearance measurements that contains helpful information on gas detector thresholds for different gases and a convenient table to fill in when making measurements. Download it now by filling out the form below.
Our seminars
Within the framework of a one-day seminar, we teach the participants – also at your site, if you wish – the necessary technical knowledge for clearance measurement according to DGUV Principle 313-002. We talk about legal basics as well as about hazardous substances and the corresponding measurement technology. Practical exercises are also part of the seminar.
In addition, we offer a two-day seminar in cooperation with the Oldenworx company to train the inspection of a manhole in addition to the clearance measurement. In particular, the correct handling of the mobile access systems is taught in practical situations.
The functional test mentioned above may only be carried out by qualified personnel according to leaflets T 021 and T 023. We also teach participants how to do this in a specially created seminar on “Equipment maintenance“.
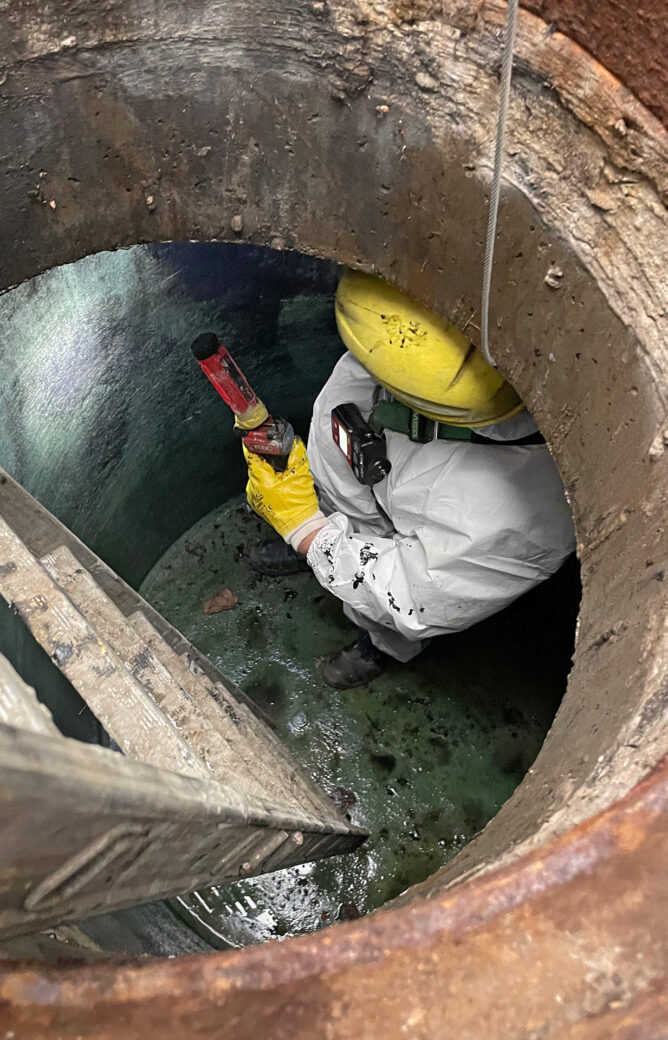