Table of Contents
Some of our customers have reported that they have problems with the pressure drop test to check whether PE pipes are free of air. The results of the pressure drop test were implausible, as otherwise all indications of sufficient absence of air were given. We have also carried out contraction procedures on (usually) sufficiently air-free pipes several times and were unable to pass the pressure drop test because too much water volume had to be drained to produce the specified pressure drop. These discrepancies were reported to us mainly during pressure tests using the contraction method on PE pipes with small drain volumes (< 10 litres), but can also occur in principle with larger volumes.
We have worked intensively on this subject and would like to clarify a few things here, describe problems and provide assistance for carrying out the pressure drop test.
What is the purpose of the pressure drop test in general?
The pressure drop test is used in hydrostatic pressure tests to check the residual air in the test section that has already been filled with water. Insufficient air absence can falsify the final result of the test procedure (see also here). The regulations usually set a target for the pressure drop to be achieved, e.g. 3.2 bar pressure drop for PE 100 SDR 11 in the contraction method according to DVGW W 400-2. There is an upper limit for the actual water volume V_ist that is drained to generate this pressure drop: the permissible drain volume V_zul. If too much water has to be drained during the pressure drop test (V_ist > V_zul), there is too much air in the pipe according to the regulations, i.e. the pressure drop test is failed and the smart memo gives the message : “Test failed. Too much air!”.
Since the update of the DVGW W 400-2 worksheet, only digital water meters/flowmeters that transmit the measured value directly to the test device (e.g. the smart memo) are permitted to carry out the pressure drop test on “result-assessing test devices” to determine the drained water volume. So here there is no longer any possibility to change the measured value of the water volume. This is probably the reason why the following problems did not occur or were noticed a long time ago.
Subscribe to our newsletter and stay informed
If you would like to be kept up to date with changes to regulations, new products, news on the blog and much more, please fill in the form below.
What are the possible reasons for a failed pressure drop test?
Pressure drop testing is not a simple process. It is also susceptible to manipulation and error (more on this below). From our point of view, it is not a good method to check for residual air, but it is currently required by the regulations. We recommend the use of air volume determination with smart memo and MPP 30-30 motor test pump as a reliable method for checking the absence of air.
We list reasons below (sorted by frequency from “often” to “rarely”) that lead to a failed pressure drop test:
1. Too much air in the pipe
In fact, it often happens in practice that there is too much air in the pipeline. The air can collect, for example, in branches, T-pieces, culverts or uneven sections of the pipeline. In unfavourable conditions, it cannot be removed by flushing, so that only pigging the pipeline can help (more on this here).
2. Contraction effects due to unfavourable operation of the drain valve/ball valve
through extensive test measurements we were able to observe effects in the pressure drop test which negatively influence the result, i.e. too much air is falsely indicated. This is not a fault of the measurement technology, but a systematic error of the pressure drop test itself. More about this in the next section.
3. Water meter/flow meter not flushed
Our flow meters of the type EDS2-V 4-160l/min 5% for the smart memo and the MPP used as well as the pressure hoses should be sufficiently flushed and completely filled with water before starting the test. If there is air in the measuring tube of the EDS2-V or large air cushions are pressed through the EDS2-V during the pressure release process, a measurement error may occur. The MPP and the pressure hoses should also be free of air. If the entire system is sufficiently vented, such measurement errors will not occur. Instructions for venting the accessories can be found here and further down in this article.
4. Water meter/flow meter has too large a measurement deviation
Our flow meters of the type EDS2-V 4-160l/min 5% for the smart memo are carefully calibrated at our factory using a reference standard, which is based on national standards in accordance with ISO 9001. The measuring accuracy of the EDS2-V fulfils the requirements of worksheet W 400-2 and in our own experience the results are reliable. In individual cases, even with the greatest care, faulty calibrations or de-adjustment during operation can occur. However, this is only very rarely the case and can be fixed by recalibration at the factory.
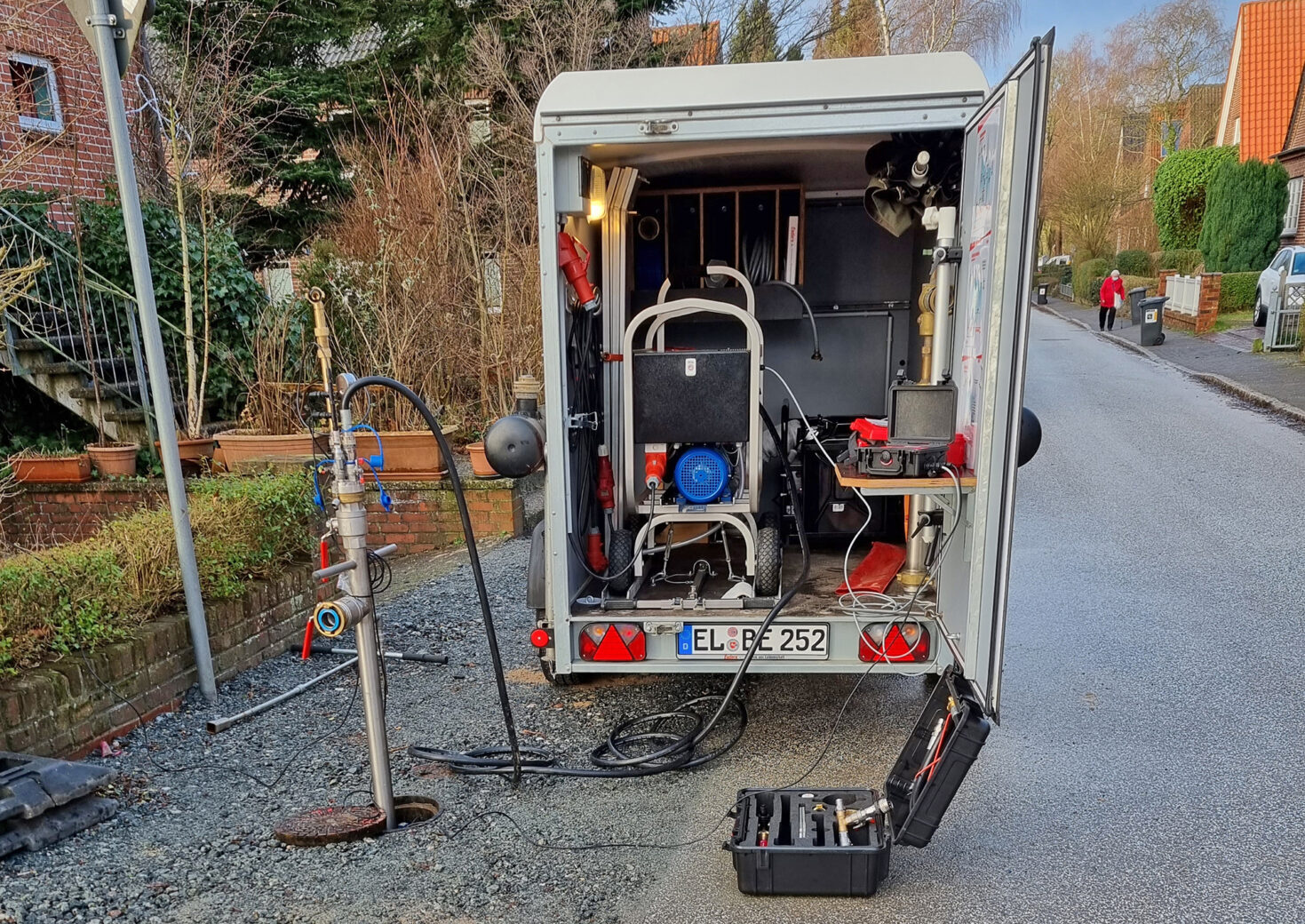
What else can happen during the pressure drop test and falsify the result?
As already mentioned in the previous section in point 2, we were able to observe effects in the pressure drop test through extensive test measurements that lead to a falsely negative evaluation of the pressure drop test, i.e. too much water volume must be drained although the absence of air is actually sufficient.
The contraction procedure as a whole is complex and takes into account the viscoelastic properties of the pipeline material, i.e. expansion of the pipeline under pressurisation (pressure keeping phase and rest phase) and contraction of the pipeline after depressurisation. The characteristic contraction behaviour of the pipeline material is used in the main test to evaluate the tightness directly after the pressure drop test has been carried out. But does the contraction of the pipe only start AFTER the end of the pressure drop test? Does the contraction start only AFTER the ball valve is closed? We have found that the contraction of the pipe may start while the pressure drop test is still in progress (i.e. while the water is still being drawn off) and may therefore falsify the result of the pressure drop test. We will publish the details of this in the near future.
Ultimately, the premature onset of contraction leads to a pressure increase, which counteracts the pressure drop caused by the water intake. As a result, too much water has to be taken out to create the given pressure drop.
This effect is a systematic error of the pressure drop test and is currently not taken into account in worksheet W 400-2. The effect does not occur in every test, but is amplified by the following circumstances:
- more relevant for small drain volumes than for large drain volumes
- “slow” closing of the ball valve at the end of the pressure drop test
- closing the ball valve for a short time or reducing the flow during water intake.
Recommended action for carrying out the pressure drop test
To avoid or minimise this effect, please be sure to observe the following recommendations for carrying out the pressure drop test:
- Open the ball valve once to create a sufficiently large flow
- Do not “readjust” the ball valve, avoid reducing the flow at all costs. Do not make any further changes to the ball valve
- Wait until the smart memo beeps and sends a text message indicating that the pressure drop has been reached
- Close the ball valve quickly and “abruptly “
The “target pressure” may be exceeded, i.e. a larger pressure drop may be generated. The smart memo always recalculates the permissible drain volume based on the actual pressure drop and then compares it with the actual drain volume. So there is no problem waiting for the smart memo to make a signal.
This recommendation does not apply to large pipe volumes and correspondingly large drain volumes (V_zul > 50 litres). In this case, there is a risk of a pressure surge in the pipe if the ball valve closes abruptly, which can then spread as a pressure wave.
Regardless of the pipe volume, the entire system should be free of air before starting the test so that later problems in the pressure drop test are avoided. For this purpose, some points must be observed already when connecting the individual, water-bearing components (MPP, EDS2-V, hoses), which we would like to explain briefly.
The MPP should be connected to a barrel filled with water or to a hydrant. Then the pressure hose between the MPP and the test head/standpipe is connected to the MPP, but not yet attached to the test head. Before this, the hydrant is opened and the MPP is allowed to run in manual mode at approx. 20 % (this process should be carried out over a longer period of time).
Only when it can be ensured that there is no residual air in the system is the pressure hose attached to the test head and both ball valves on the test head are opened. The turbine (EDS2-V) must also be connected to the test head. Now the test stand tube can be filled via the previously flushed system. For this purpose, the MPP is again operated in manual mode at low power (max. 20 %) until water flows out of the turbine (this process can also be carried out over a longer period of time). As soon as the water flows out of the turbine without any bubbles, the pump should be switched off for 10-20 seconds, as turbulent water in the standpipe can move upwards to the turbine during this period. Then the pump should be turned on again for a few seconds at max. 20 % power in order to lead the residual air out of the system.
EDS2 automatic water drain
Even when using the EDS2 automatic drain, the water quantity can be influenced by the effect described above during the closing process of the automatic valve. The closing process of the automatic drain is not abrupt, but is carried out gradually in order to avoid pressure surges. Due to the gradual reduction of the flow, the contraction of the pipe starts and the evaluation of the pressure drop test may be falsified.
With the release of new software for the smart memo, we have optimised the valve control for the EDS2 automatic drain to reduce and, if necessary, compensate for the impact of this effect (in accordance with the equations given in worksheet W 400-2). Thus, we can recommend the use of the EDS2 automatic water drain to avoid errors.
To use the optimised control, the device software on the smart memo must be updated (latest version v123 dated 21.07.2023). You can do this easily via the Esders Connect app.
Are you encountering difficulties with pressure decay testing of PE pipes?
Our experts can help you resolve the issues and ensure efficient performance of pressure decay testing. Do not hesitate to contact us! We will find a suitable solution to your challenges, request a consultation.
We will get back to you promptly if you give us your contact details.