Table of Contents
Purging gas pipelines is a regular process as part of repair work as well as commissioning and decommissioning. This involves either letting gas into a new or repaired pipeline or removing it from a pipeline that is already in operation. The latter is often referred to as inertisation, as the pipe is usually purging with an inert gas to displace the fuel gas. Inert gases are gases with a very slow (chemical) reactivity. The formation of an explosive mixture is therefore virtually impossible – unlike with air or oxygen. The noble gases helium, xenon and argon, for example, are inert gases. In the gas industry, nitrogen is usually used as an inert gas as it is relatively cheap.
What is the recommended flow velocity during the purging process?
In both cases – during gassing and degassing/inertisation – it is important to measure the flow velocity in the pipe. According to DVGW G 465-2, the velocity should ideally be between 3 and 7 m/s during the purging process. This is to achieve a turbulent flow, i.e. a turbulence with which the fuel gas is completely displaced from the pipe.
If the flow velocity is below 3 m/s, there is a risk of laminar flow, in which layers of fuel gas and inert gas can form. As these layers do not mix, it is possible that the fuel gas is not completely removed from the pipe and individual “fuel gas cushions” remain in the pipe. The physical properties (density, viscosity) of the different gases play a role here.
On the other hand, at a speed of more than 7 m/s, there is a risk that dust or dirt particles in the pipe will be carried along and cause sparking. In the worst case, this could ignite a potentially explosive gas-air mixture during a purging process with air.
Difficulties in measuring flow velocity
However, it is not always possible to maintain the aforementioned purging speeds, as a considerable amount of gas is required to achieve a speed of 3 m/s, especially with large nominal pipe diameters. In addition, there are usually constrictions in the system, such as tapping clamps, ball valves or other fittings, which prevent a sufficiently high flow rate. For this reason, there is a reference to purging velocities in accordance with DIN EN 12327 in the appendix to G 465-2, where a minimum purging velocity of 0.6 m/s is required.
What methods are used to measure flow velocity in a gas pipeline?
How can the flow velocity in the pipe be measured? Until now, this was usually done with an explosion-proof pressure gauge, which was attached to the upper end of the blow-out pipe or the outlet of the pipeline. However, this is relatively unwieldy and inaccurate, and blowing out natural gas is no longer permitted due to the new EU Regulation on methane emission reduction. Instead, it is better from an environmental point of view to flare the excess gas.
Mobile gas flares are used for this purpose, which are an effective tool for reducing operational methane emissions in accordance with DVGW G 404. However, the use of an anemometer with a flare is more than questionable from a safety point of view. Other methods are therefore more appropriate and safer.
Use of mobile gas flares and gas measuring devices to determine the flow velocity
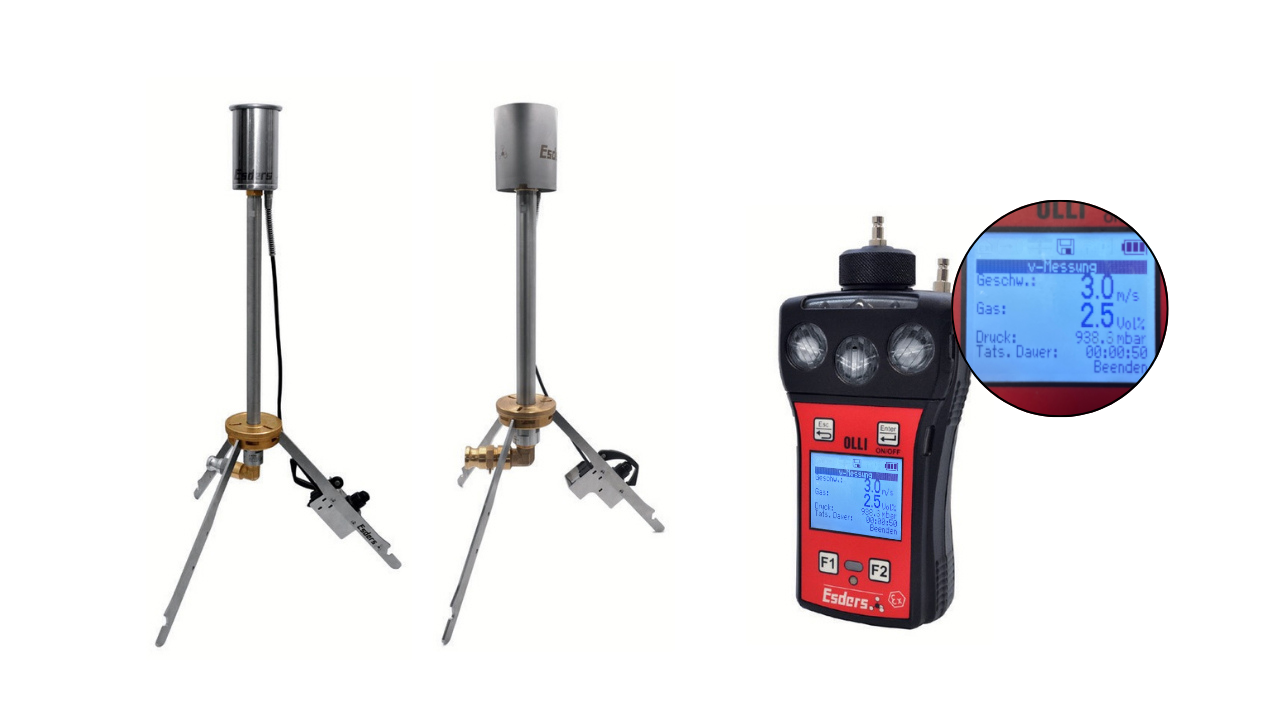
Esders GmbH currently offers two mobile gas flares in different performance classes. In combination with the OLLI gas measuring device in the appropriate configuration, the velocity in the pipe can be determined much more precisely. To do this, it is necessary to enter information about the purging process (e.g. gas type, pipe dimensions, pressure) into the device before the measurement begins or to measure this during the purging process. Together with the characteristic curve stored in the measuring device for the respective gas flare used, the OLLI determines the purging velocity in the pipe and shows this as a value in m/sec on the display.
Advantages of flow velocity measurement with OLLI
This allows the user to regulate the purging process, for example by opening or closing the ball valve at the beginning of the pipe to allow more or less (inert) gas to flow into the pipe. As the velocity is measured at the outlet of the pipe and there can be several hundred metres between the beginning and end of the pipe during purging processes, at least two employees are required. One person stands at the beginning of the pipe and operates the ball valve, the second person stands at the end of the pipe and controls the flow rate and the mobile gas flare. Both employees must be in contact with each other ( by radio, telephone, etc.).
With this method, it is possible to monitor the gas concentration at the outlet of the pipe – without having to use additional technology or personnel – and thus make a statement about the gas concentration (gassing) or absence of gas (degassing/inertisation) in the pipe. This is also a requirement of G 465-2. A further advantage is that this method records the quantity of natural gas/methane discharged or burnt. This data must be reported to the relevant authorities as part of the EU Methane Regulation.
We have described a specific application example with the Mobile Gas Flare S in combination with the OLLI here.
Further developments: more powerful gas flares
In addition to the Mobile Gas Flares S and M, Esders GmbH will soon launch additional gas flares with higher power (= higher flow volume). This will also make it possible to measure the flow velocity in the pipeline.
Would you like to be informed about the latest industry news and product innovations right away? Then simply sign up for our Esders newsletter using the form below.